The Six Sigma Black Belt certification verifies the candidate has the basic knowledge of the material and can demonstrate that the knowledge and abilities are transferable to other areas of the organization. There are two types of Six Sigma Black Belts. One is for Black Belts who have already earned a green belt certification, and the other is for candidates without a Six Sigma Black Belt certification. With six sigma certification, these candidates are considered professionals who are ready to step up and take on leadership responsibilities within the organization.
The advantage of six sigma certification is that it increases the candidate’s credibility and positions them as an expert. Lean strategies build on the strengths of the company and so using lean principles increases productivity, reduces waste and improves employee satisfaction. Six Sigma courses teach employees how to reduce costs, streamline procedures, create and maintain effective working relationships, and improve customer service by defining priorities. Six Sigma courses are also taught regarding human resources, customer behavior, and Lean manufacturing principles.
The Six Sigma approach promotes lean manufacturing and continuous improvement, which allow employees to feel ownership over quality improvements and the improvement of the business. In an organization with lean policies, there is no room for inefficiency. Instead, quality improves and employees feel empowered to make choices about their work. This fosters loyalty and increases the workers’ willingness to put their best efforts forth.
When employees know they are making a difference and that their contributions are making a difference, they become enthusiastic about their jobs and the organization. When you are an employee, it’s easy to get wrapped up in your job and forget about what you are really doing. When you have a Six Sigma Certification, however, you become aware of your impact on the business. When you see the difference you have made, it can’t be undone. People are willing to go the extra mile to make a difference. People aren’t just making shortcuts; they’re making a commitment to customer satisfaction and organizational efficiency.
A Six Sigma Black Belt is training to recognize problems, prioritize them, and take action. Lean Six Sigma Black Belts and Green Belt training are different; they focus on implementation and strategy. Six Sigma Black Belt training focuses on training employees on Lean Six Sigma tools and emphasizes continuous improvement strategies. Six Sigma Green Belt training focuses on improving and maintaining quality and implementing strategies to improve and maintain quality and profitability.
Black Belts are certified and obtain a certificate. Green Belts completes a course and then earn an associate’s degree or diploma. Six Sigma Black Belt training provides Black Belt certification to employees who are already doing full-time employment in an organization. Green Belt training may be required for employees working in a consulting firm, though certification is not always necessary.
Six Sigma is an evergreen methodology that has been adopted by many organizations worldwide. Because Six Sigma requires so much fewer people to execute than traditional manufacturing methods, it saves money, produces results faster, and reduces waste and non-value added expenses. Six Sigma training helps employees understand and use Six Sigma tools effectively and supports Lean manufacturing principles. Organizations with lean management philosophies are more sustainable, have lower customer turnover, and profit more.
Related Six Sgama Certifcations:
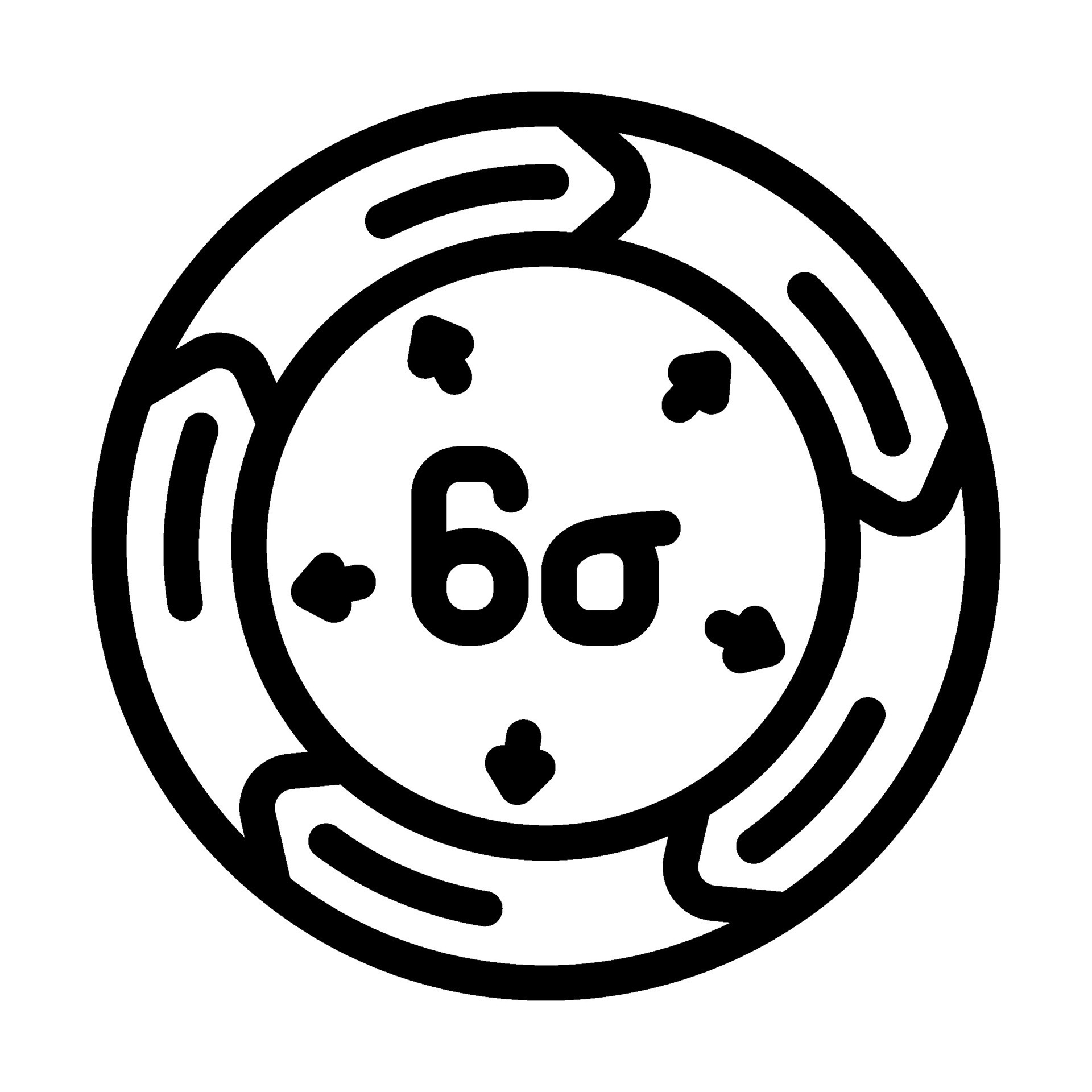
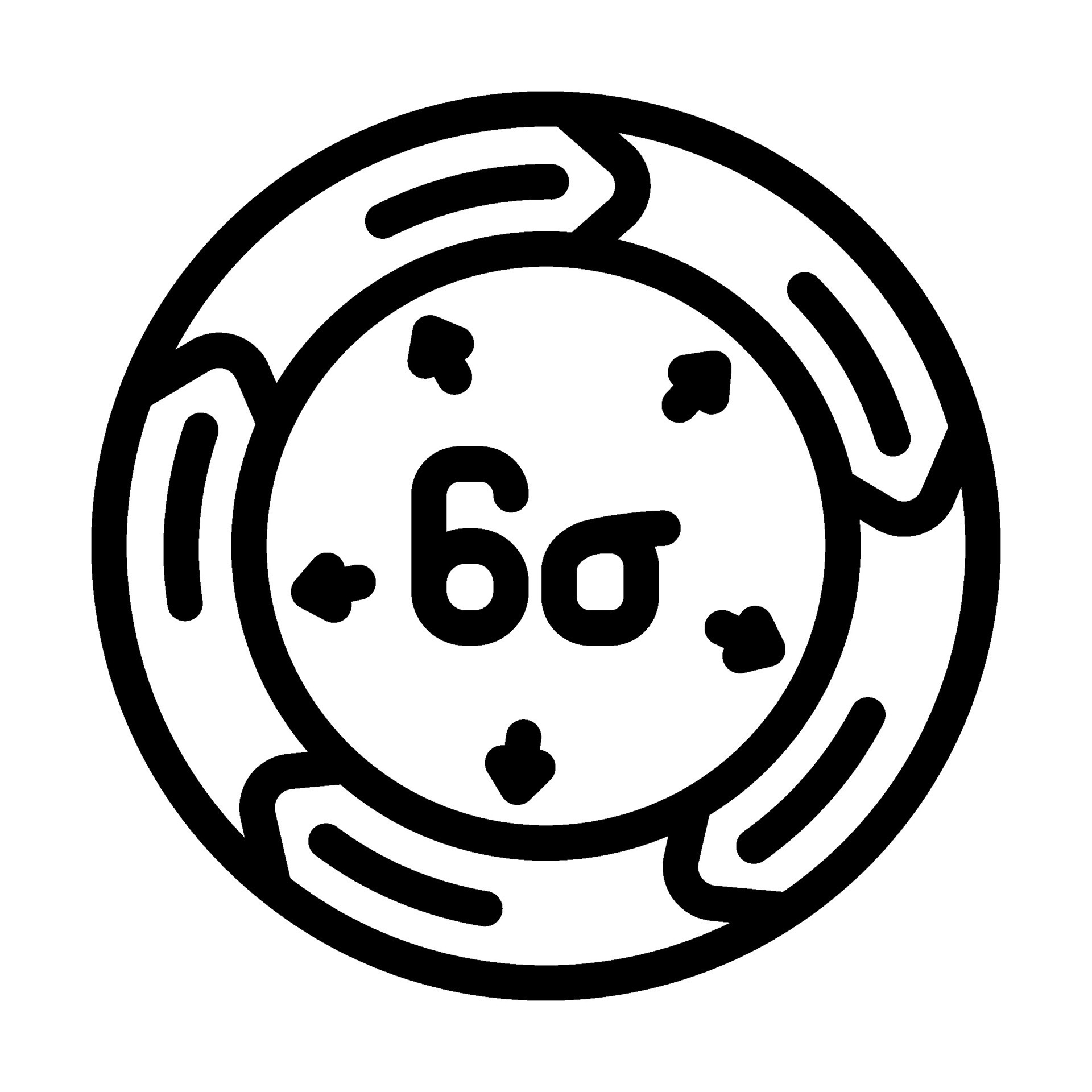
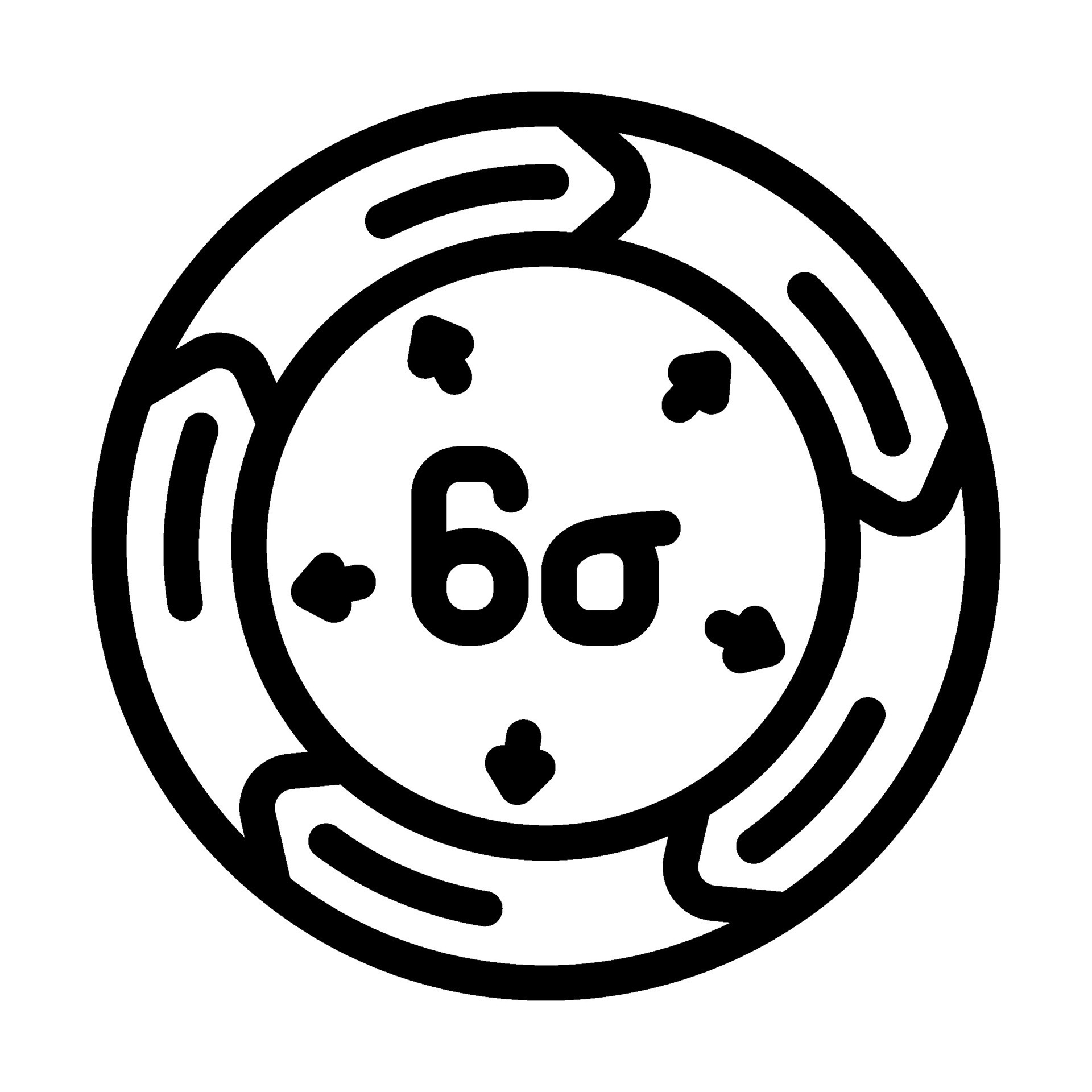
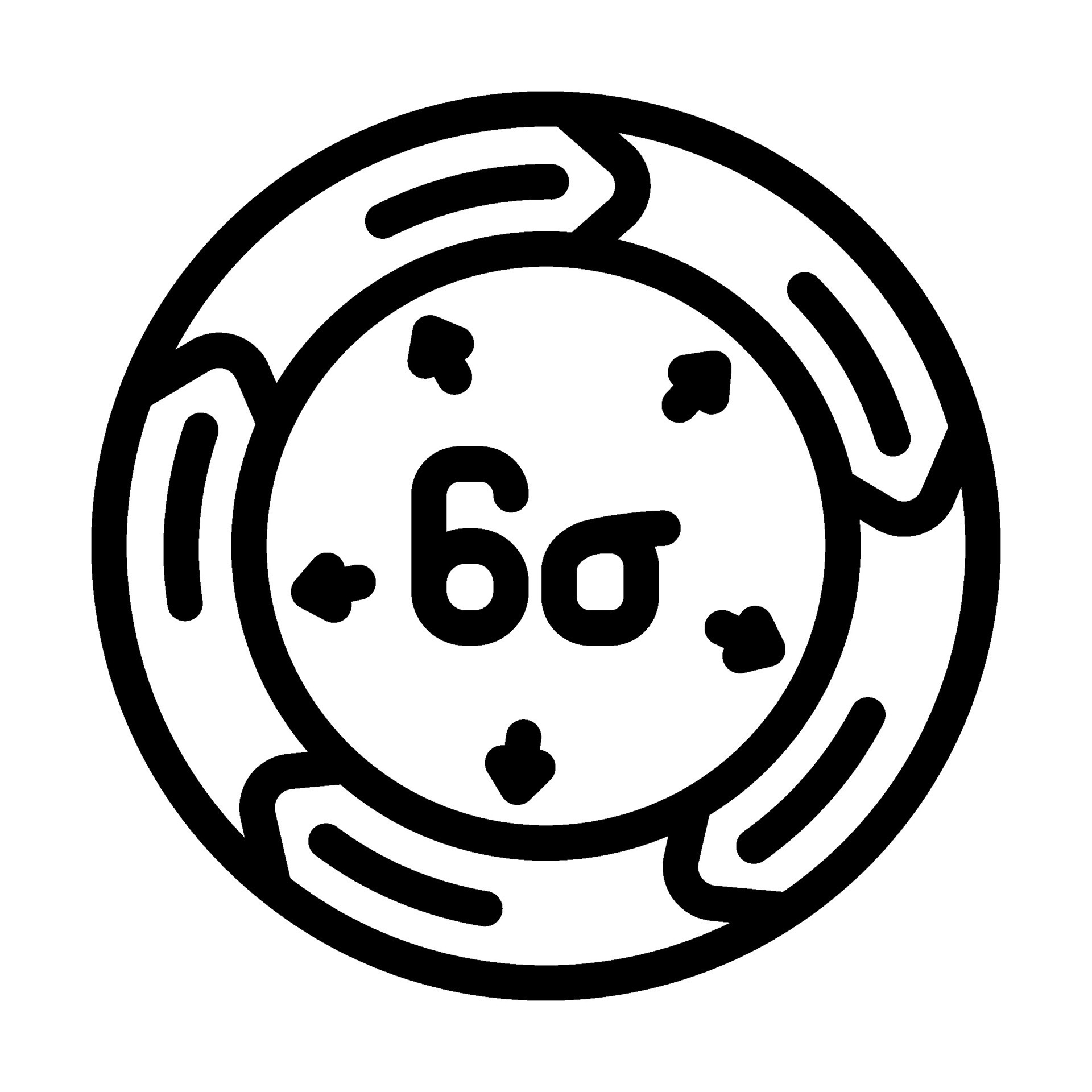
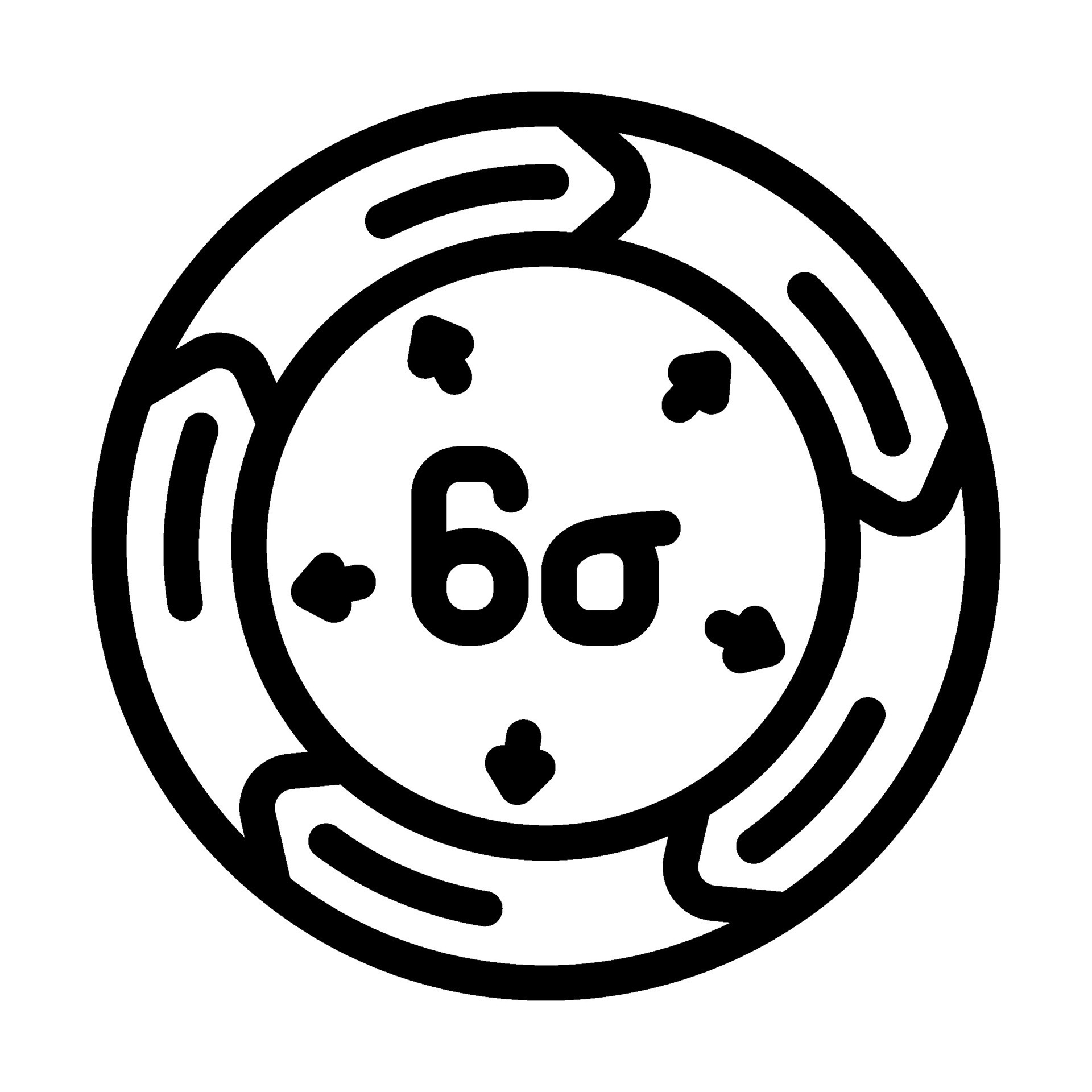
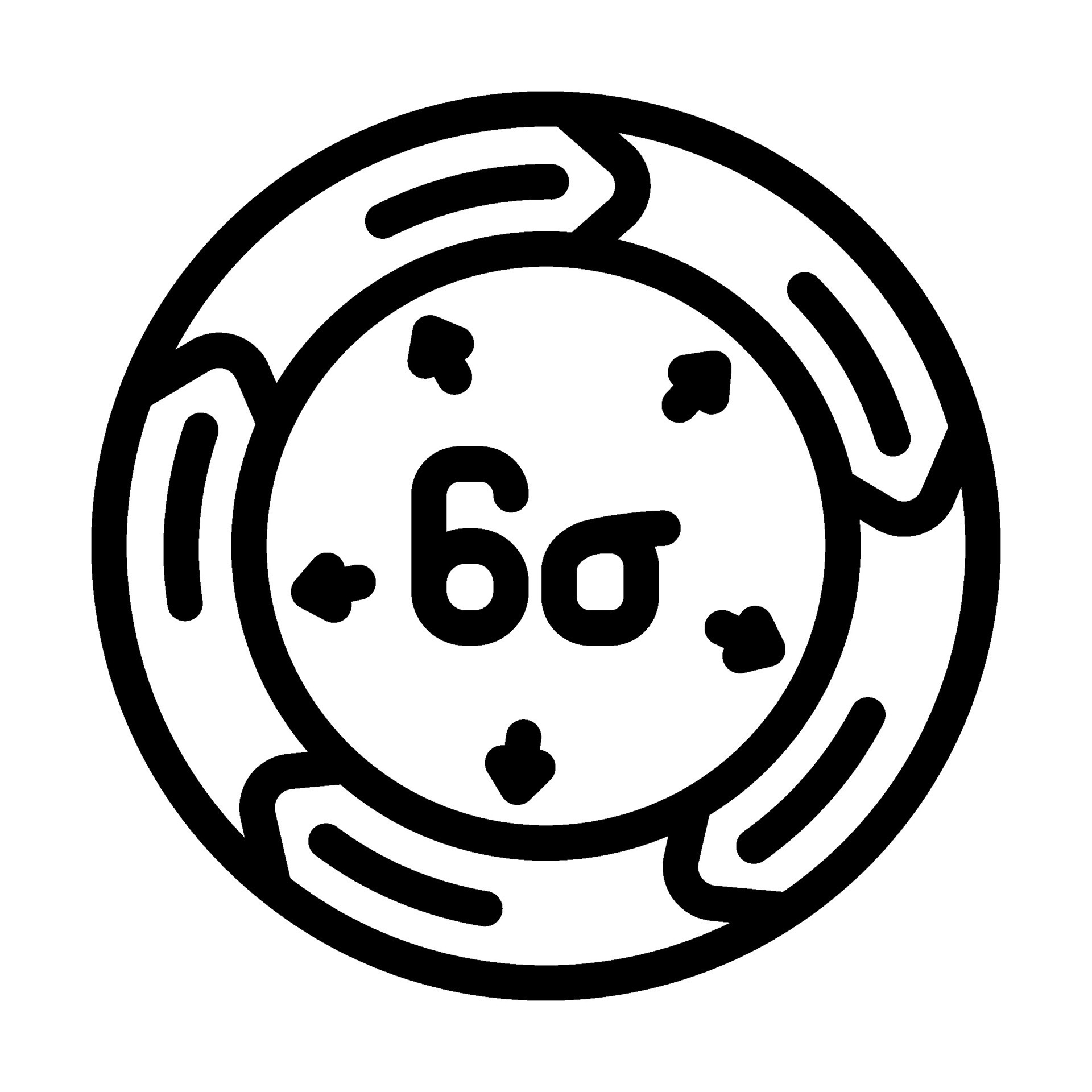
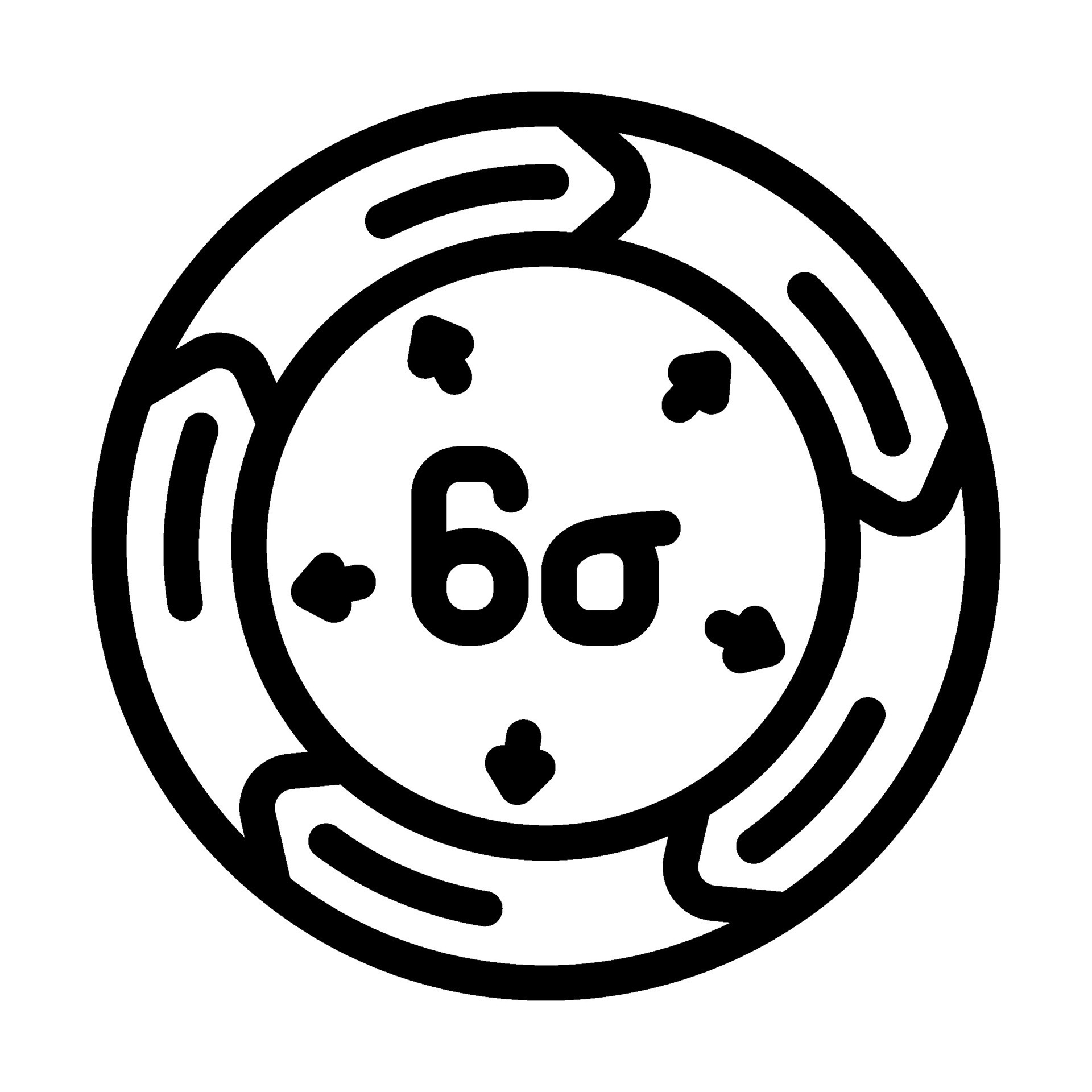
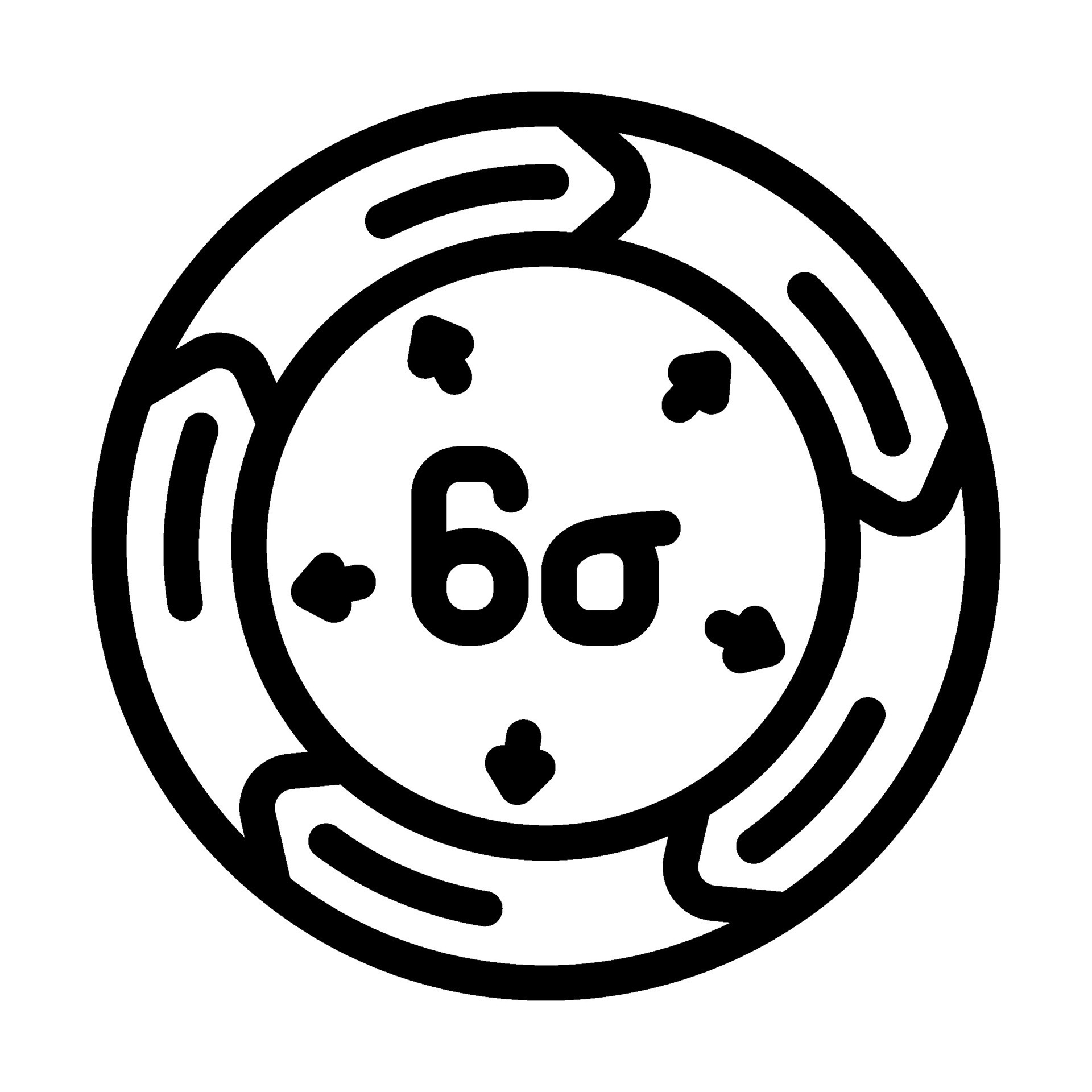
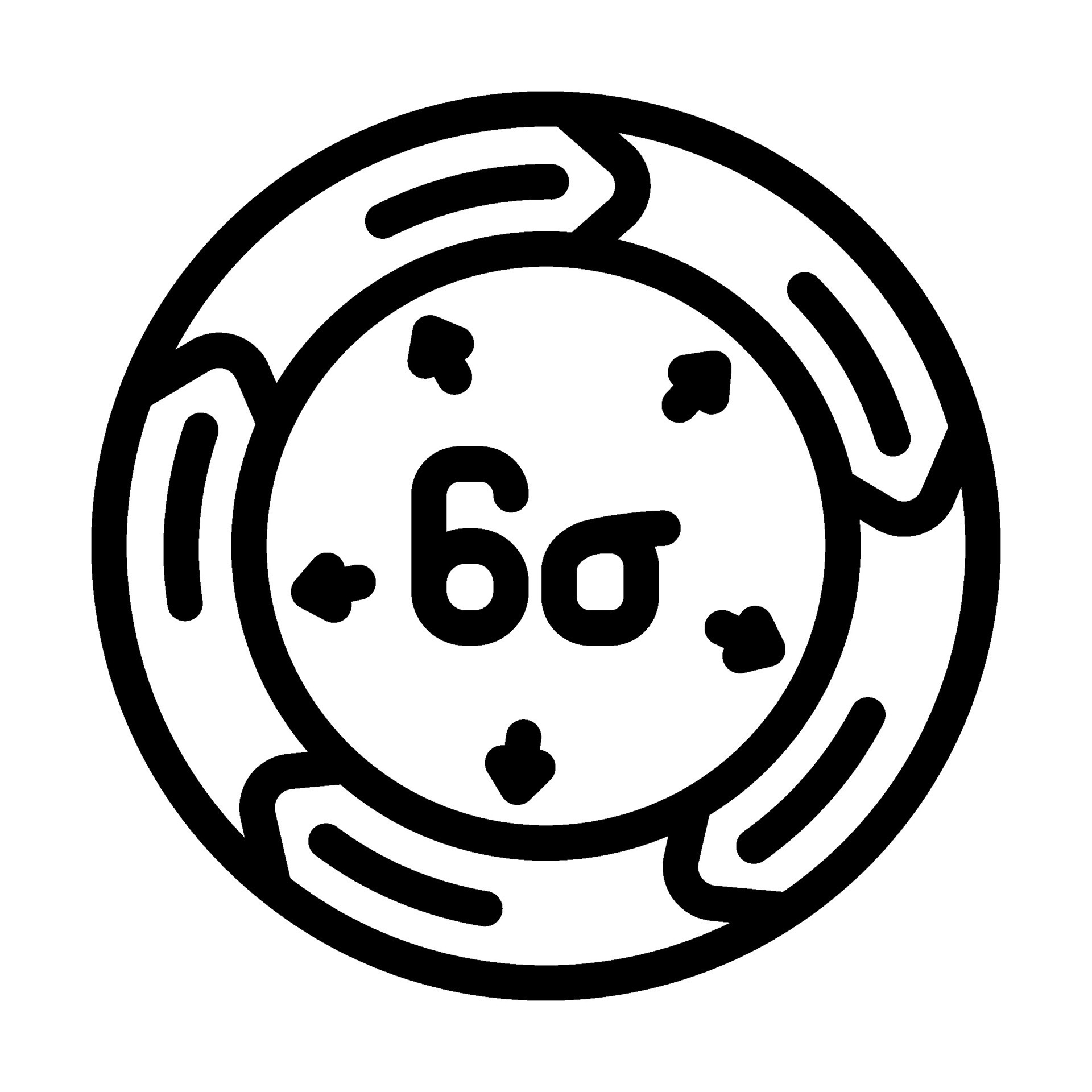
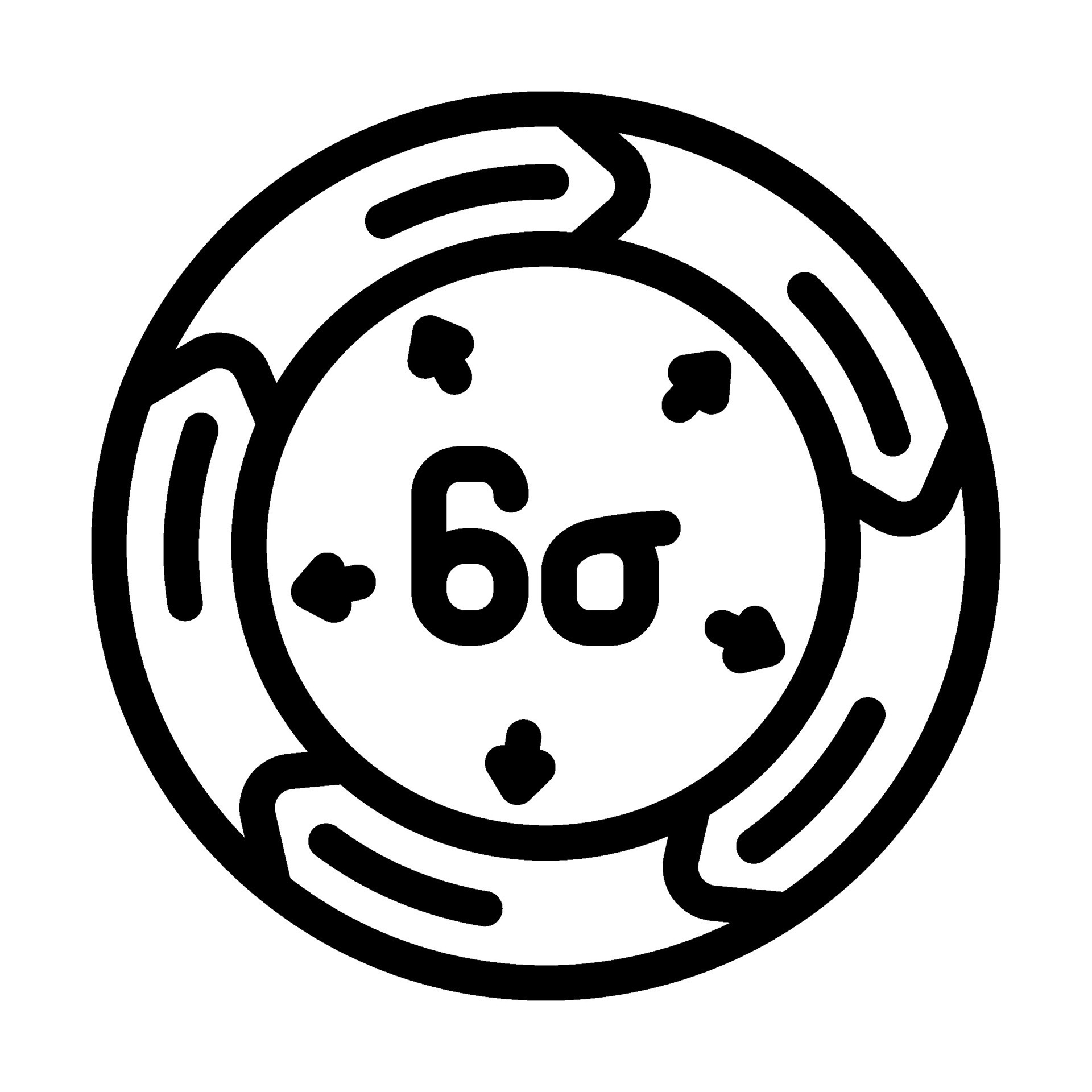