The first of the six sigma certification steps is taking a look at the organization. This can be done by going out and speaking to the staff and other individuals who are part of the business. There needs to be an honest and open dialogue about what is working and what is not. Is the organization in reaching its goals for product quality, service, and the overall efficiency of the business? If not, then something needs to change in order for things to improve.
The next set of steps pertains to the documentation. Every piece of documentation has to have a purpose and a value. This value can be quantified in some way and it can be discussed within the context of the company’s goals. It is also a means to try to quantify how well the documentation has been useful to others within the organization. Taking the time to properly document the steps and lessons learned will be very important.
The next set of six sigma certification steps looks at the tools that are used. Every employee should be trained in the use of those tools. They should also understand what makes them effective and which tools aren’t going to produce the same results as others. They should be taught how to best use them in order to do their job effectively.
Another step in the process improvement process looks at the tools that will be used to measure improvements. They will need to be made in such a way that they can be used on all parts of the entire process. Those measurements should be made over time, rather than at the beginning of the process. All employees will need to know how to make those measurements and then document them. Looking into how the process actually works, can give employees an idea of what needs to be improved and how they are supposed to go about making those improvements.
Looking into what tools and six sigma training need to be in place before the process starts is another part of the process improvement activity. There are many things that can happen in an organization once a Six Sigma course has been taught. For example, the method of measuring customer satisfaction may change. Changes in process flow may become necessary. Those are all valid issues to look into before six sigma certifications can be finished.
The best way to do this part of the process improvement activity is to have clear expectations of what Six Sigma certification will look like when it is completed. It should not be too broad. It also needs to be specifically designed to work with one business process or project. Some companies think that everyone who completes the training has the same expectations as the company, but that is rarely the case. People tend to have different feelings about what they have been taught.
Looking into what six sigma certification requirements are for the company you are working with is a good thing to do. It can help to ensure that employees understand what is expected of them. It can also help to make sure that the standards that are put into place are adequate for the area you are working in. Doing so can improve the process of your business uses for quality control, which can ultimately lead to better customer service and happier workers.
Related Six Sgama Certifcations:
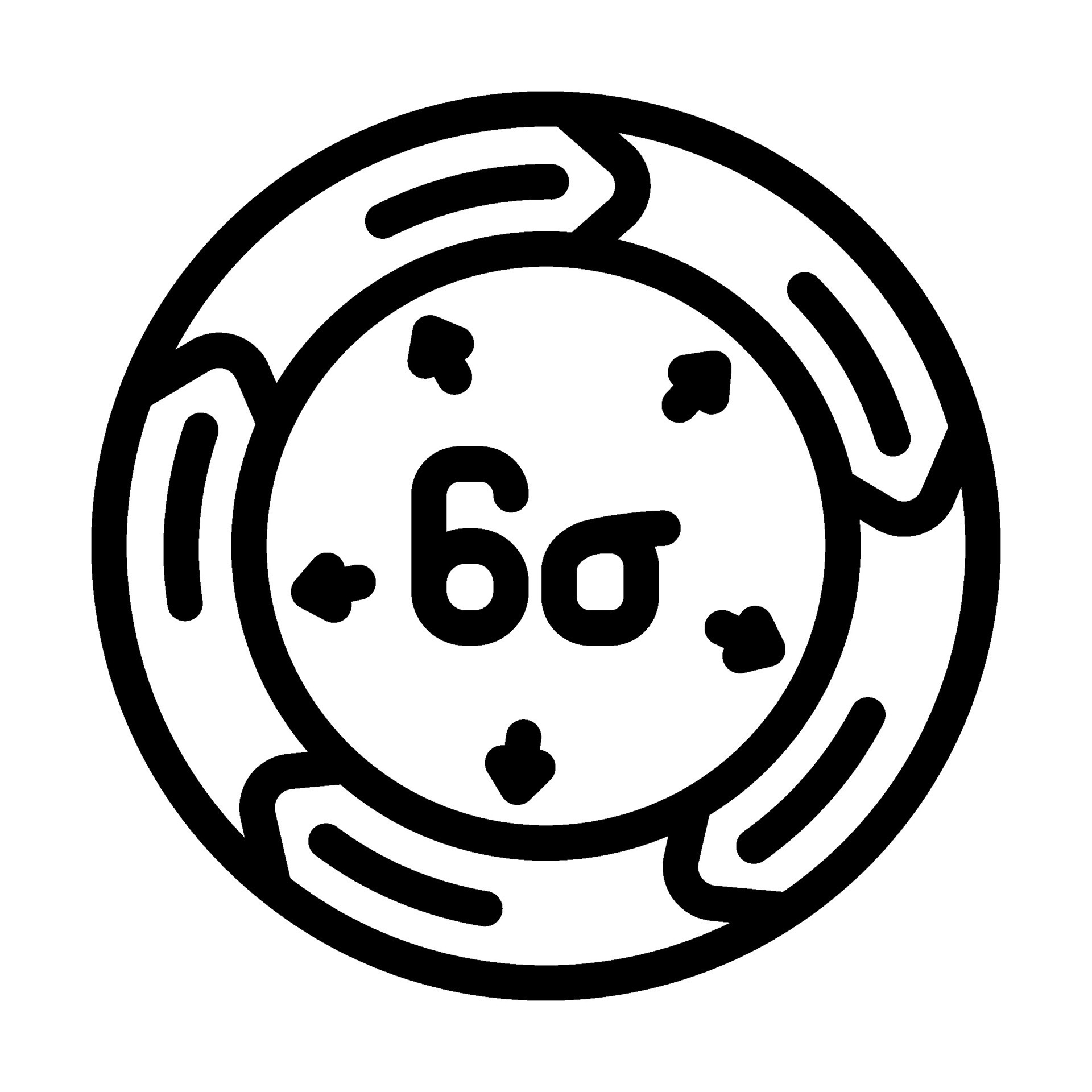
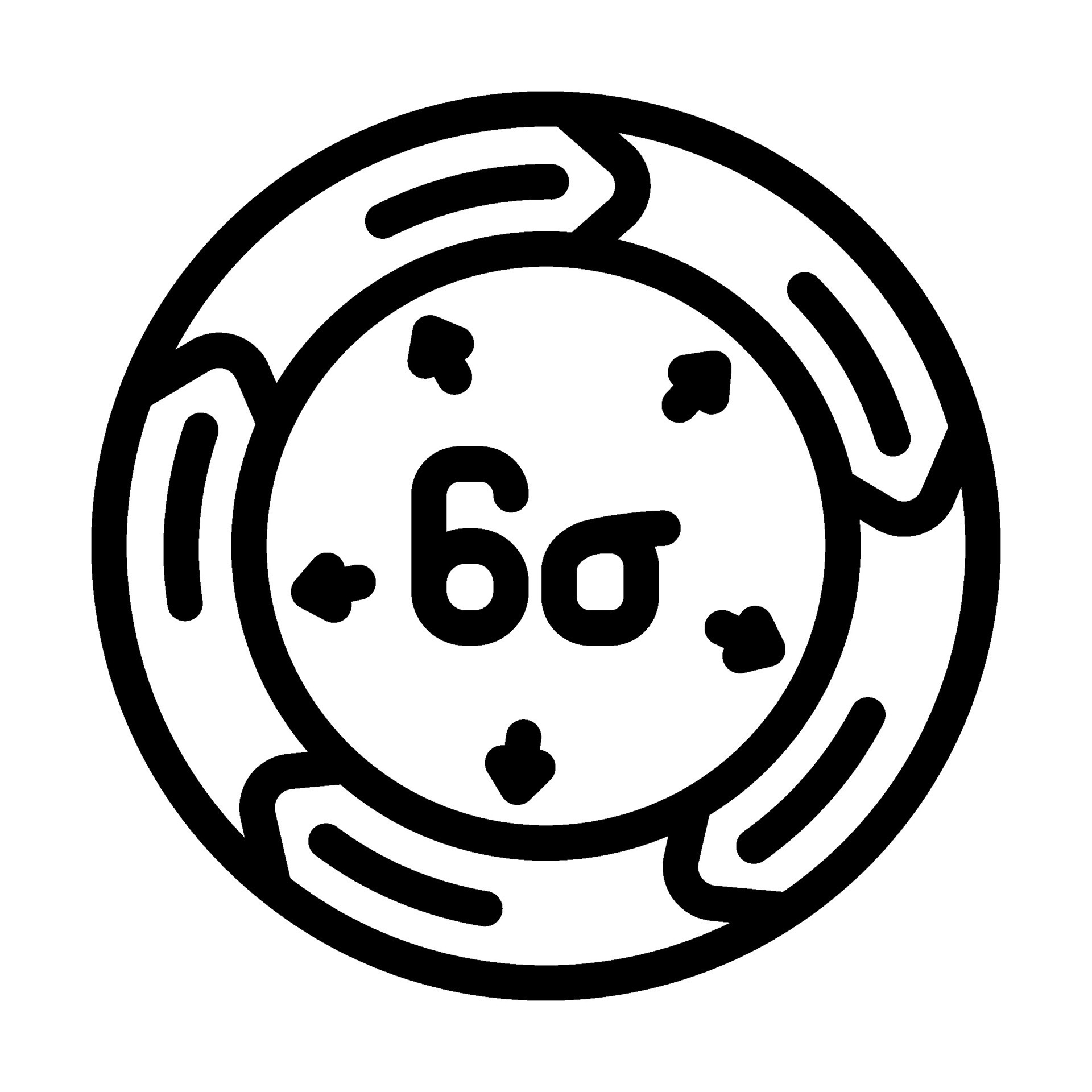
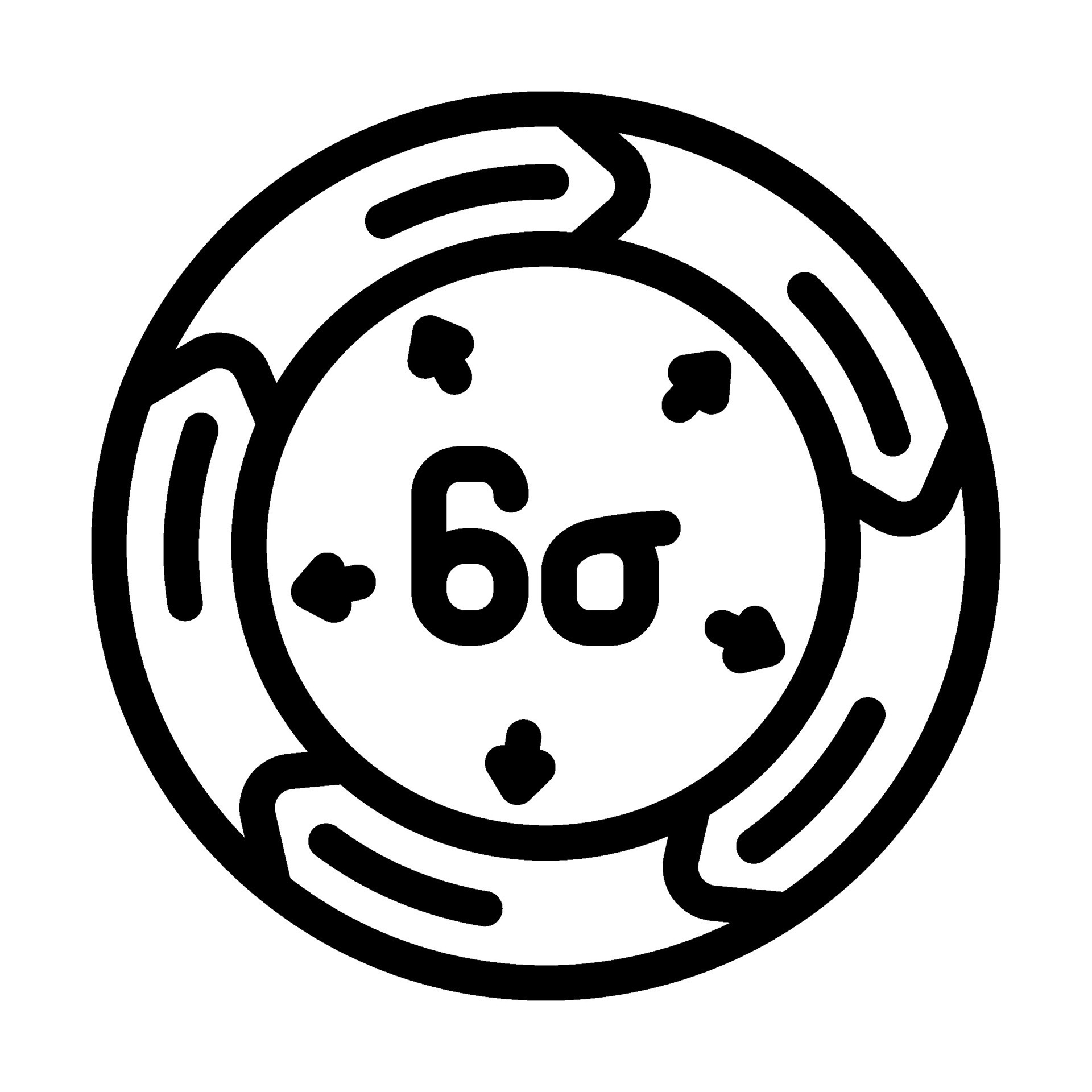
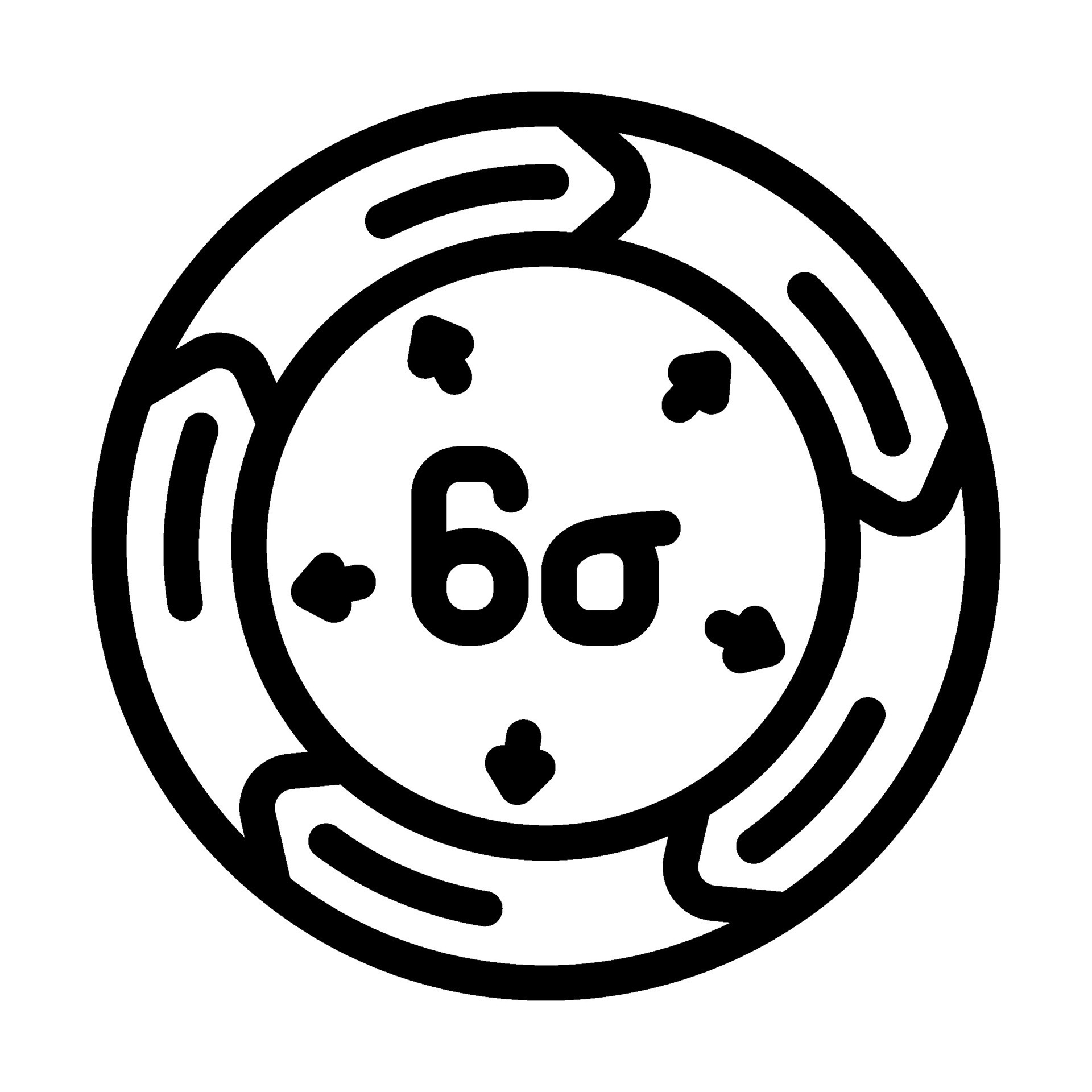
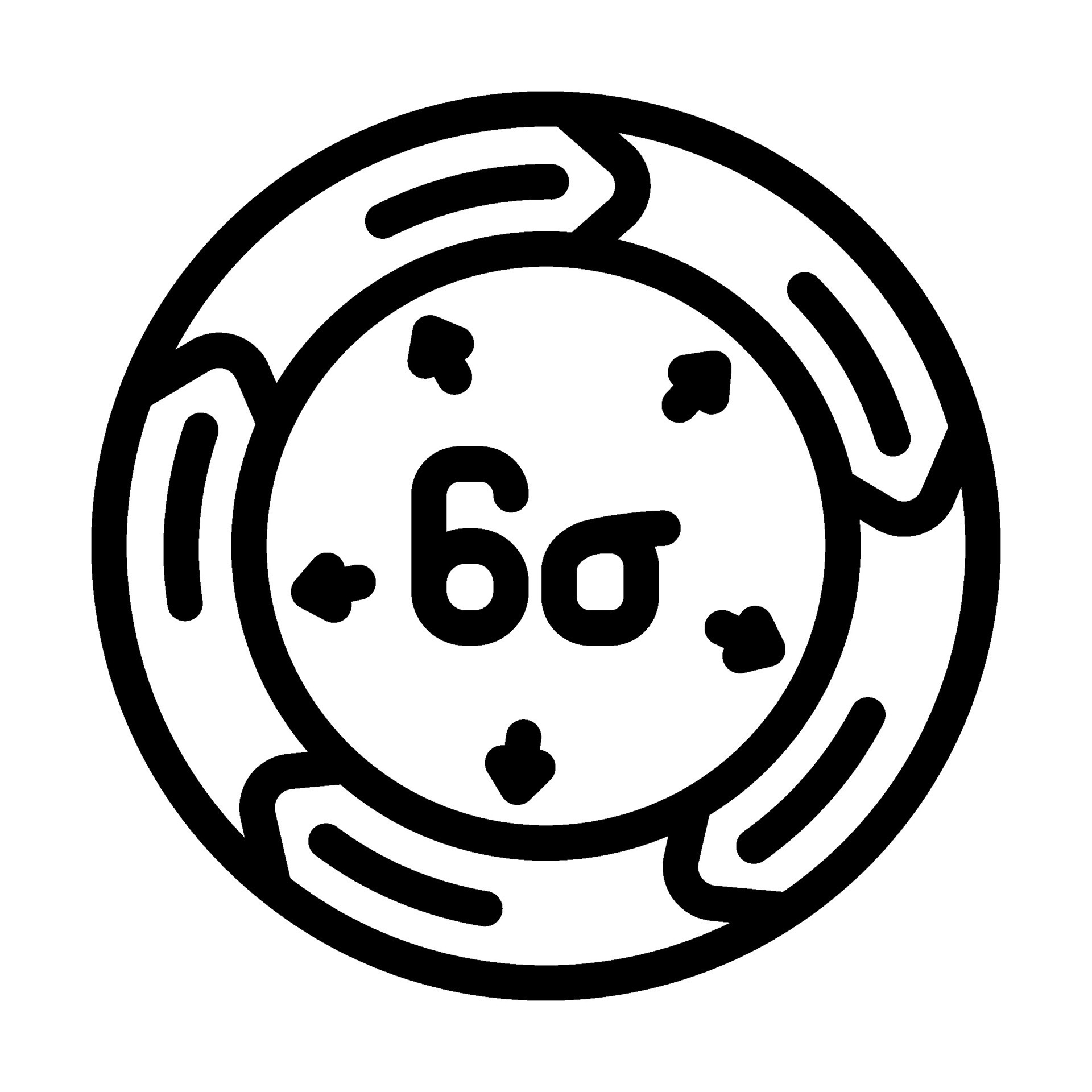
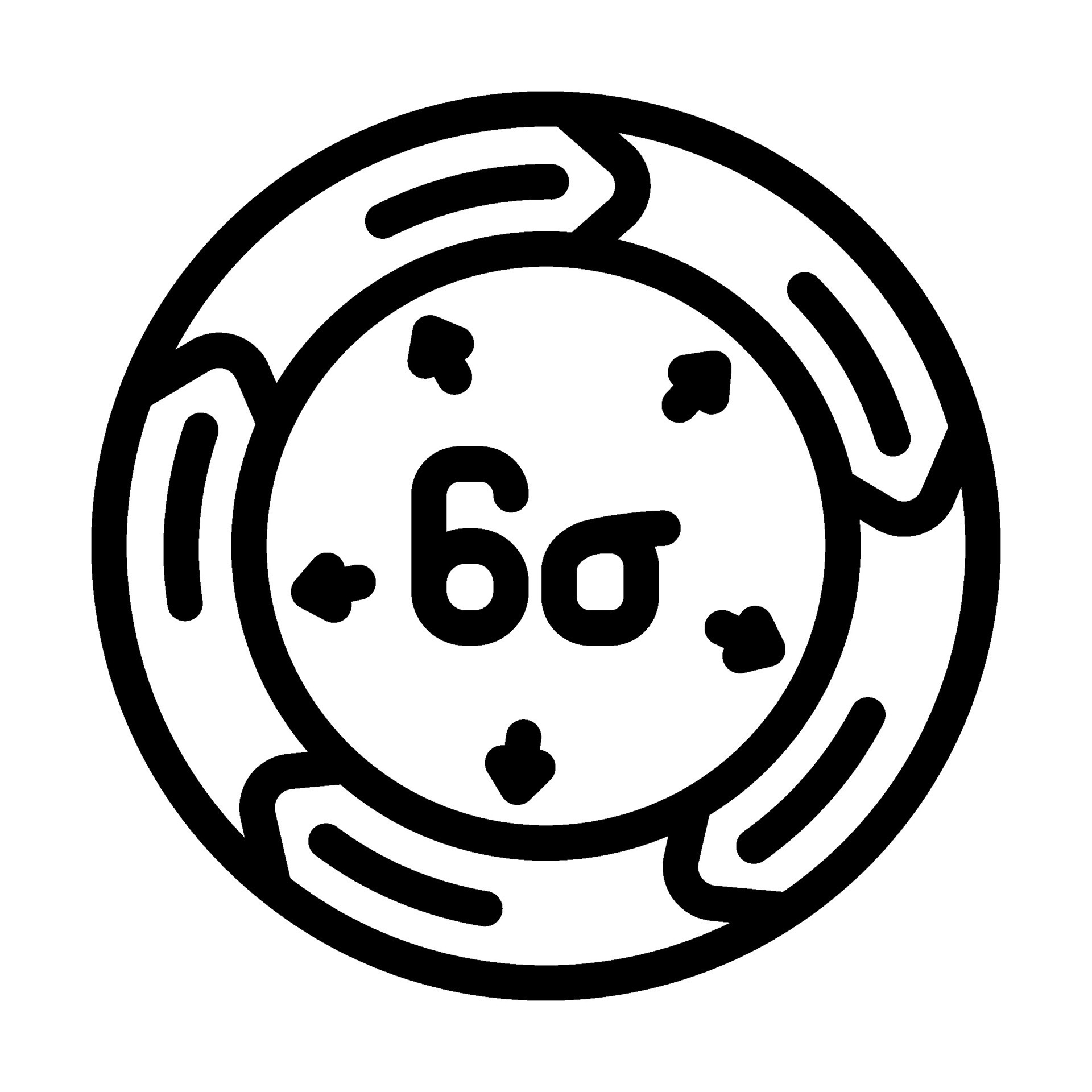
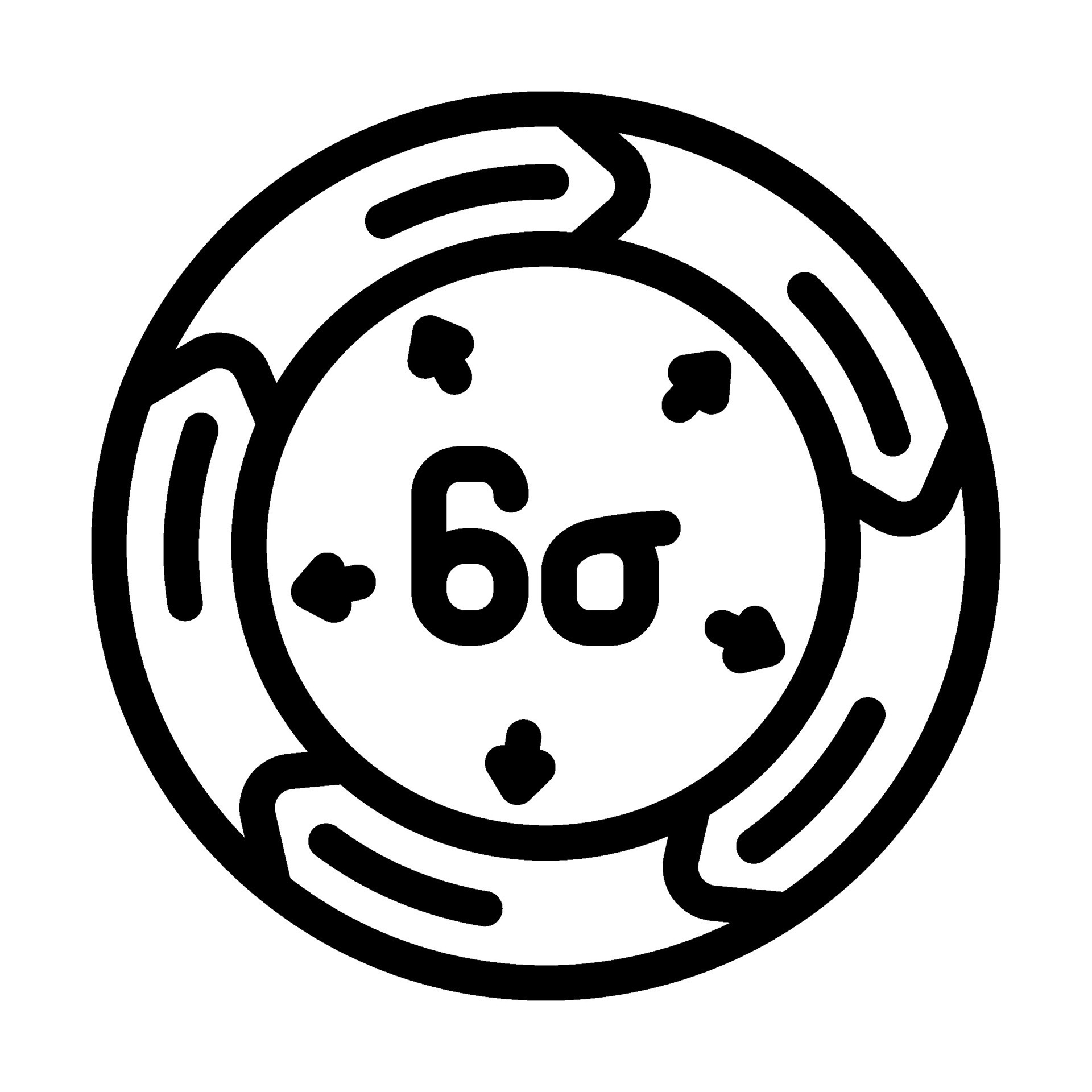
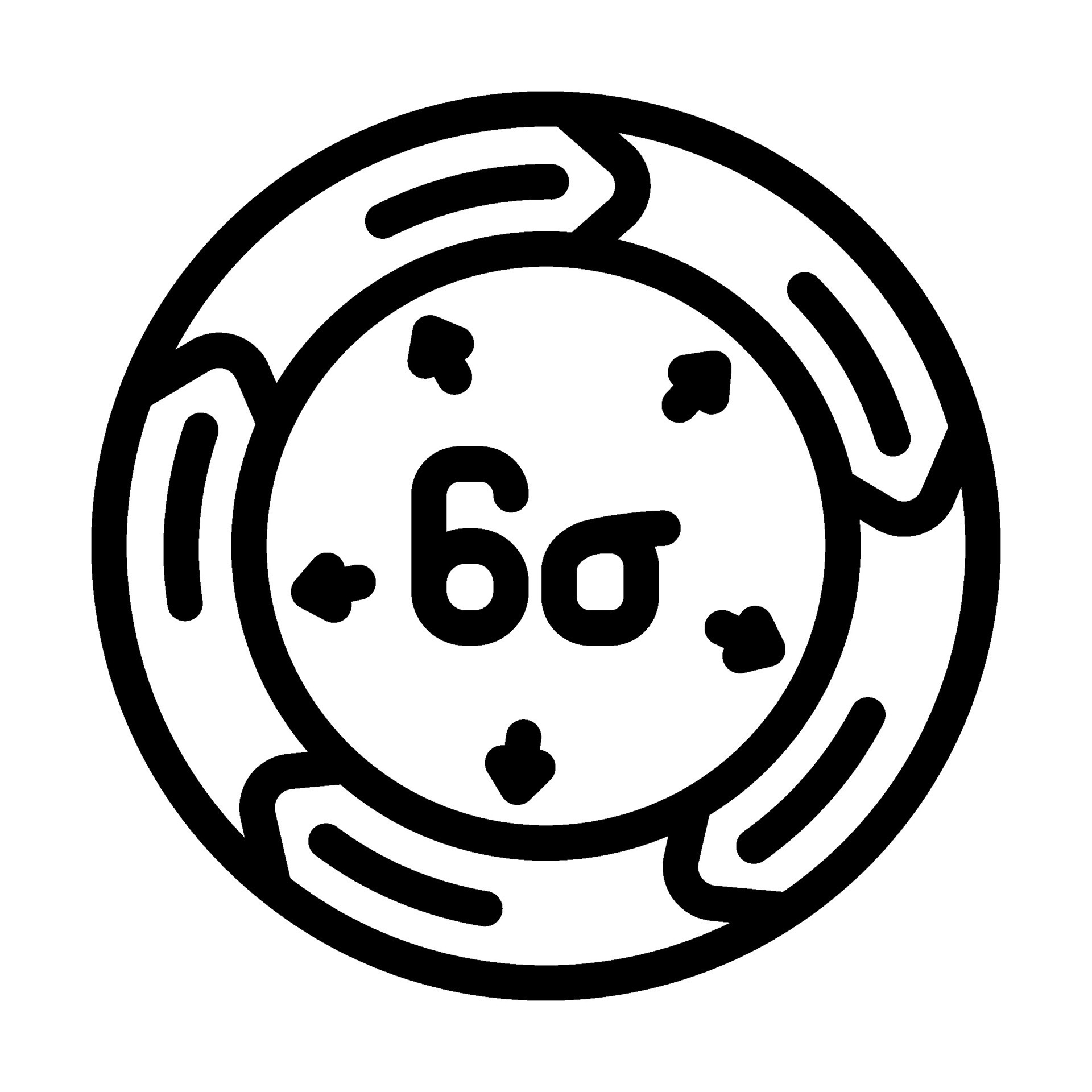
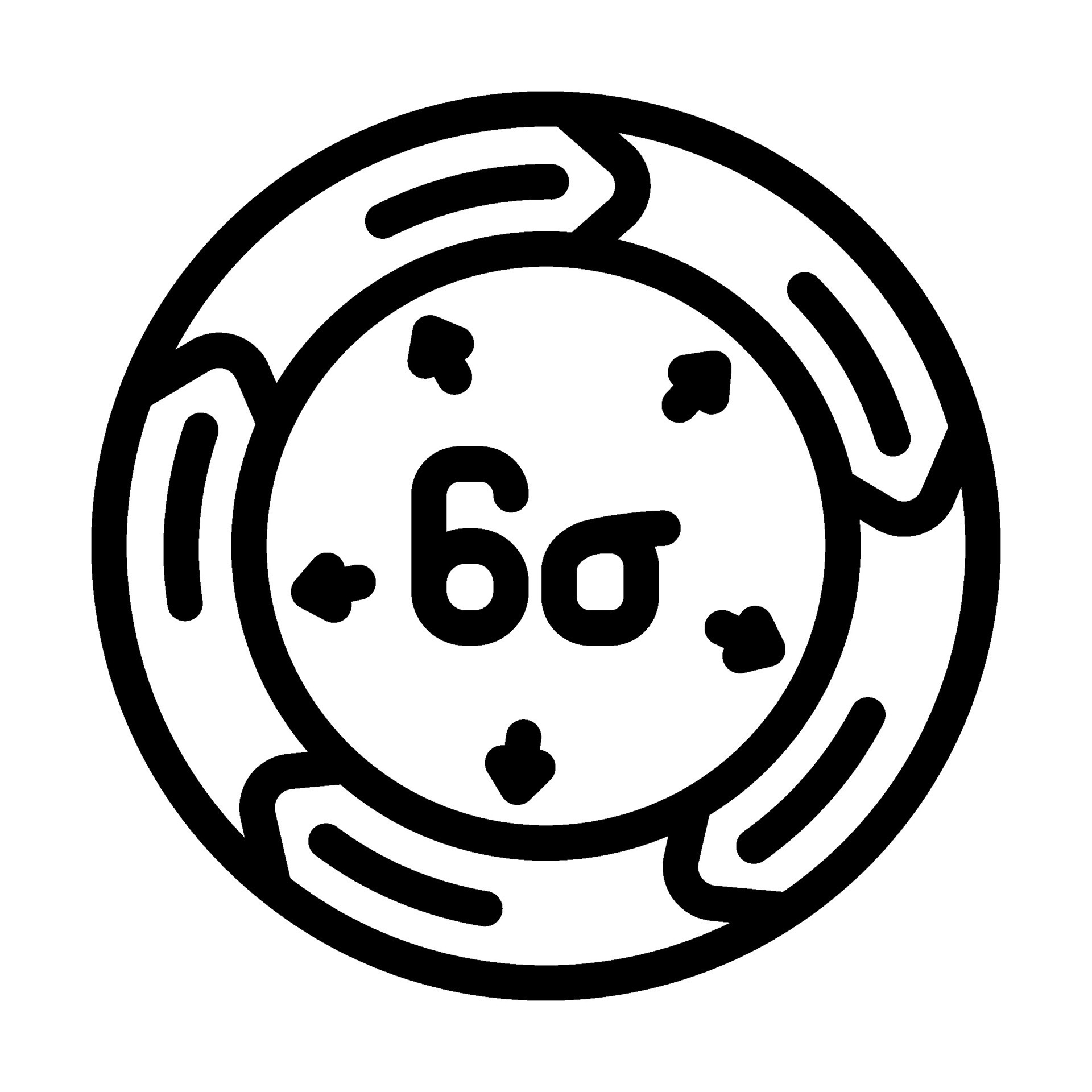
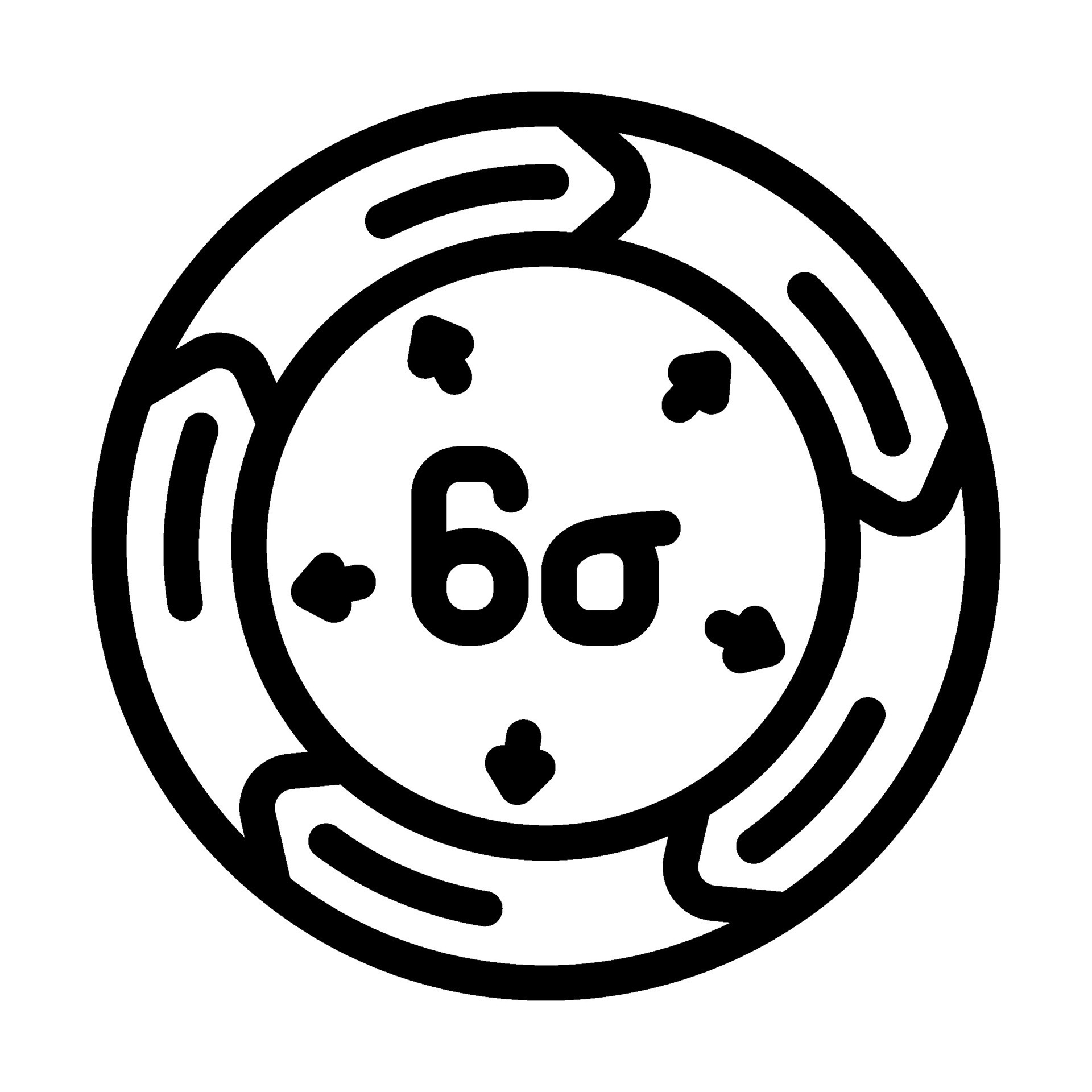