Six Sigma is broken down into three processes: Quality, Process, and Control. The Quality process is concerned with producing a high-quality product while keeping the cost down. The process part of Six Sigma is important because it focuses on making sure that processes are followed correctly, the process is accurate, and products are delivered in a timely manner. Lastly, the control part of Six Sigma ensures that the quality of the product or service is sustained throughout the delivery and helps to ensure that the product or service meets customer expectations.
In order to get the most from the Six Sigma program, the customer must first focus on the product and what it offers them. Customers should focus on getting the product right the first time. Once this is done, the customer should focus on making sure that the product or service meets all of their needs. For Six Sigma to work, the customer should focus on everything.
When the company focuses on the customer, they will be more efficient and productive in their day to day operations. In order to gain the best results, the company should work on customer satisfaction. The best way to get customer attention is to understand who the customer is and what they want from the company. Then, the company should work on meeting these needs.
Every company has processes and/or activities that they use when dealing with customers. These processes are important but sometimes they become outdated and no longer serve the purpose that they were designed for. In order to stay relevant, companies need to look at upgrading their processes.
Upgrading a process involves taking out processes that are no longer working in order to replace them with new ones that are more effective and productive. In order to do this, the company will have to go through some planning and analysis. This will take some time but will be very worthwhile once the work is done. Some companies may want to start by looking at their current processes. Once they have a list of their current processes in place, they can then go through and look at the steps that they are using to take, the steps that they have eliminated, and the steps that they are replacing with other processes.
When doing a process audit of their business processes, there are several things to look at. First, a company will want to look at the number of belt levels that exist within the process. Each belt level will have a certain amount of work that is assigned to it and will be responsible for completing that specific task. The number of levels that exist is dependent on the overall volume of processes that are being conducted by the company.
The next thing to look at is the types of functions that are performed by each belt level within the process. This will allow the Six Sigma team to figure out what types of processes are necessary in order to get the desired results from the customers’ products or services. Once this information is gathered, a plan can be developed to improve on the processes that are currently being used in order to ensure that the company gets the best results possible. Redesigning processes is often necessary in order to make a business more profitable and keep customers happy.
Related Six Sgama Certifcations:
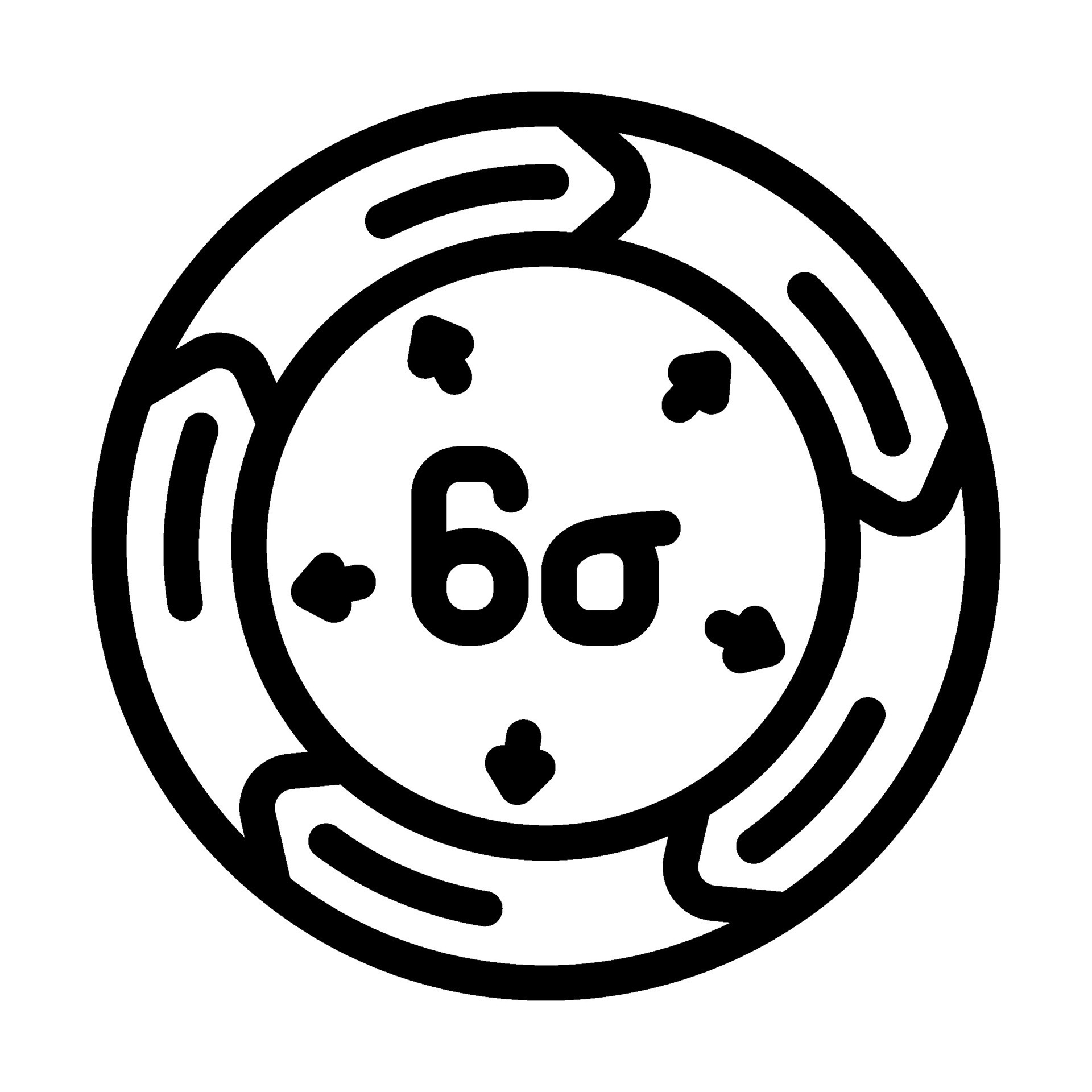
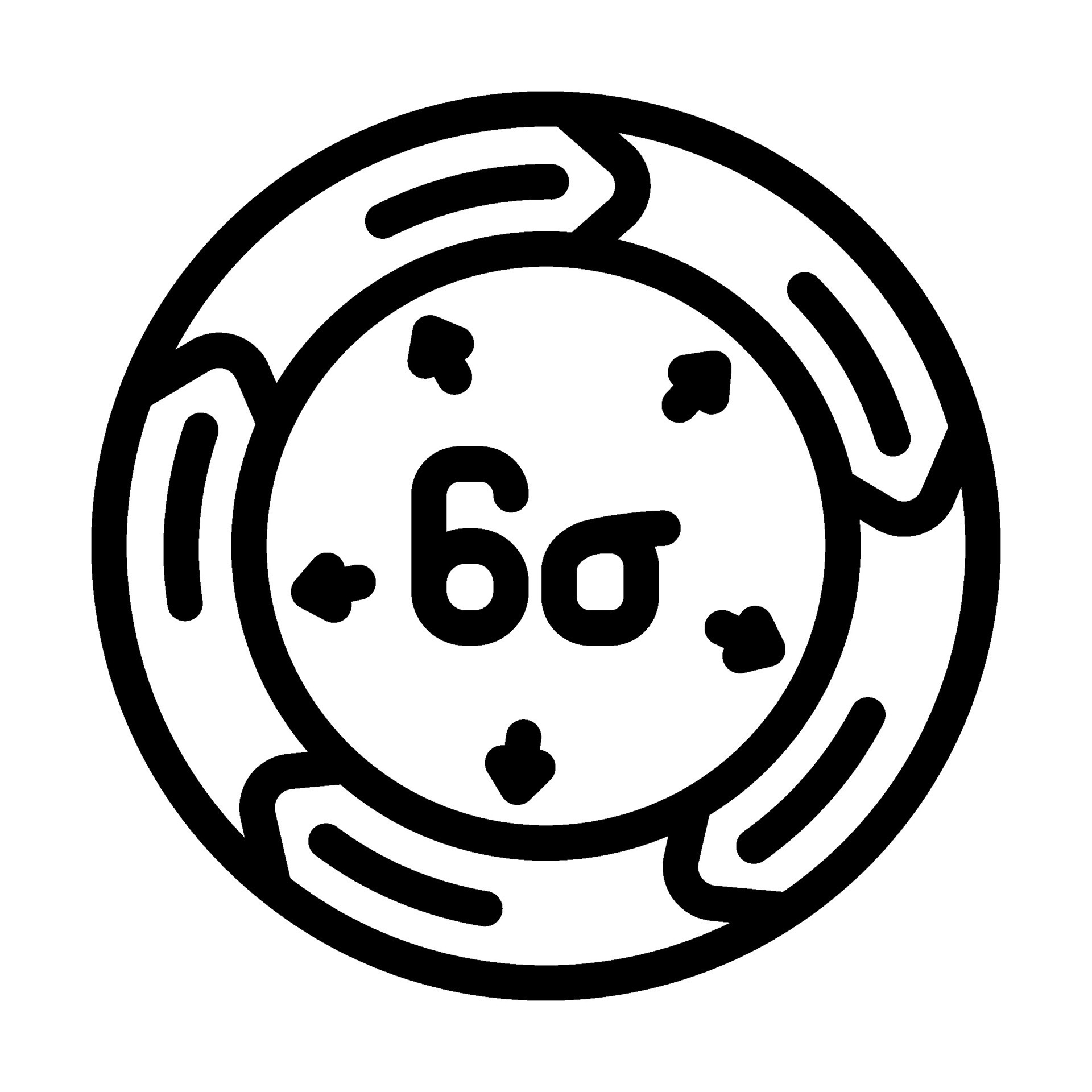
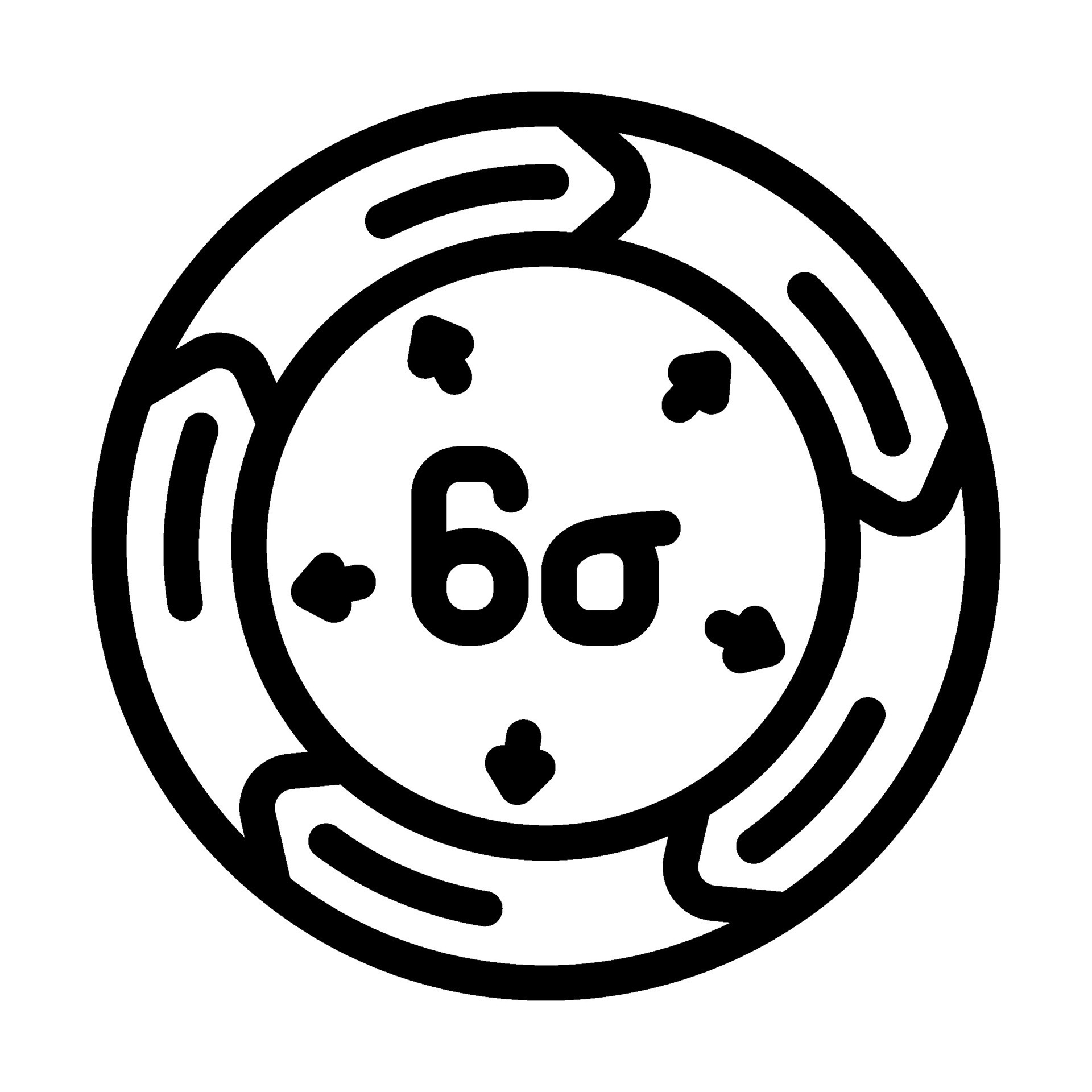
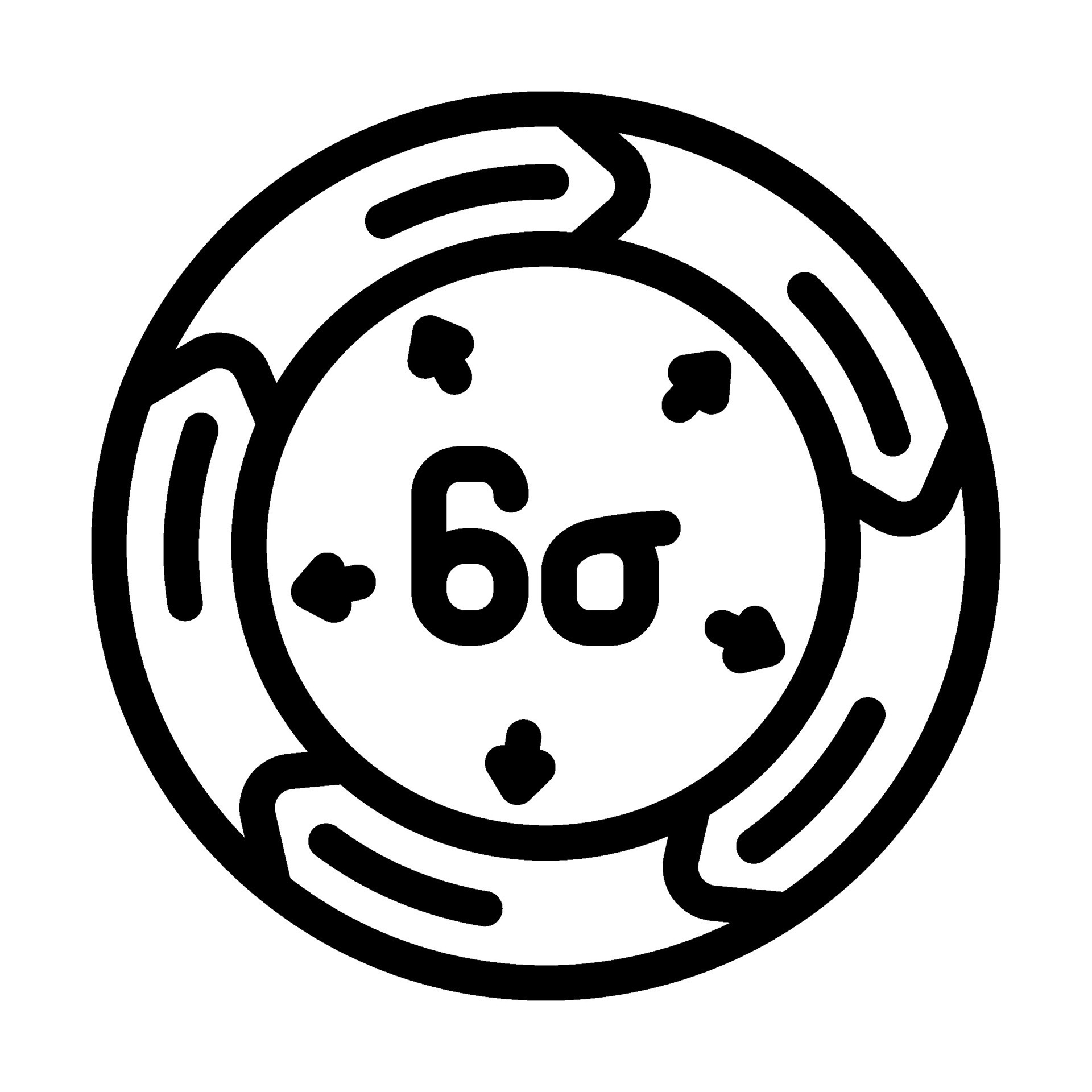
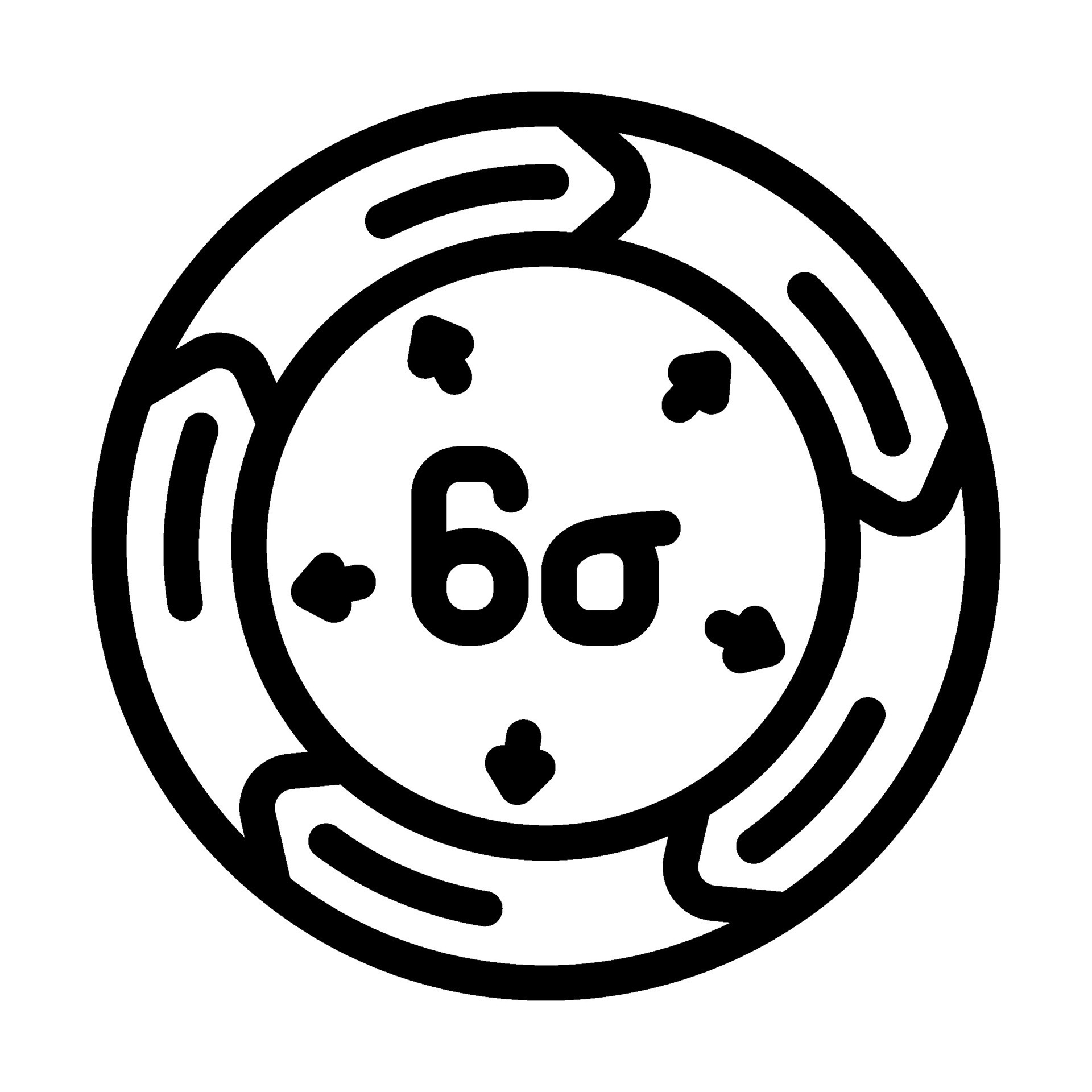
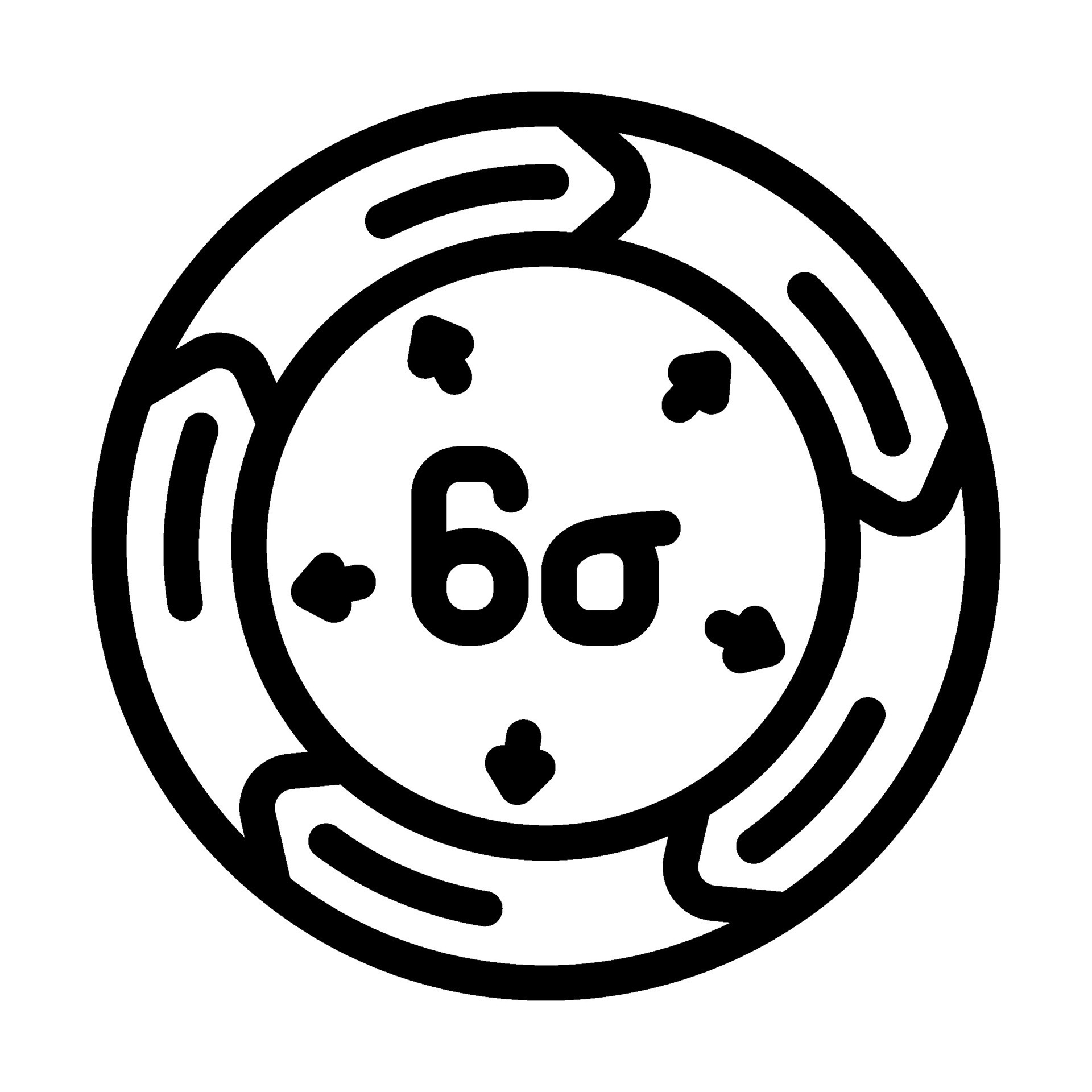
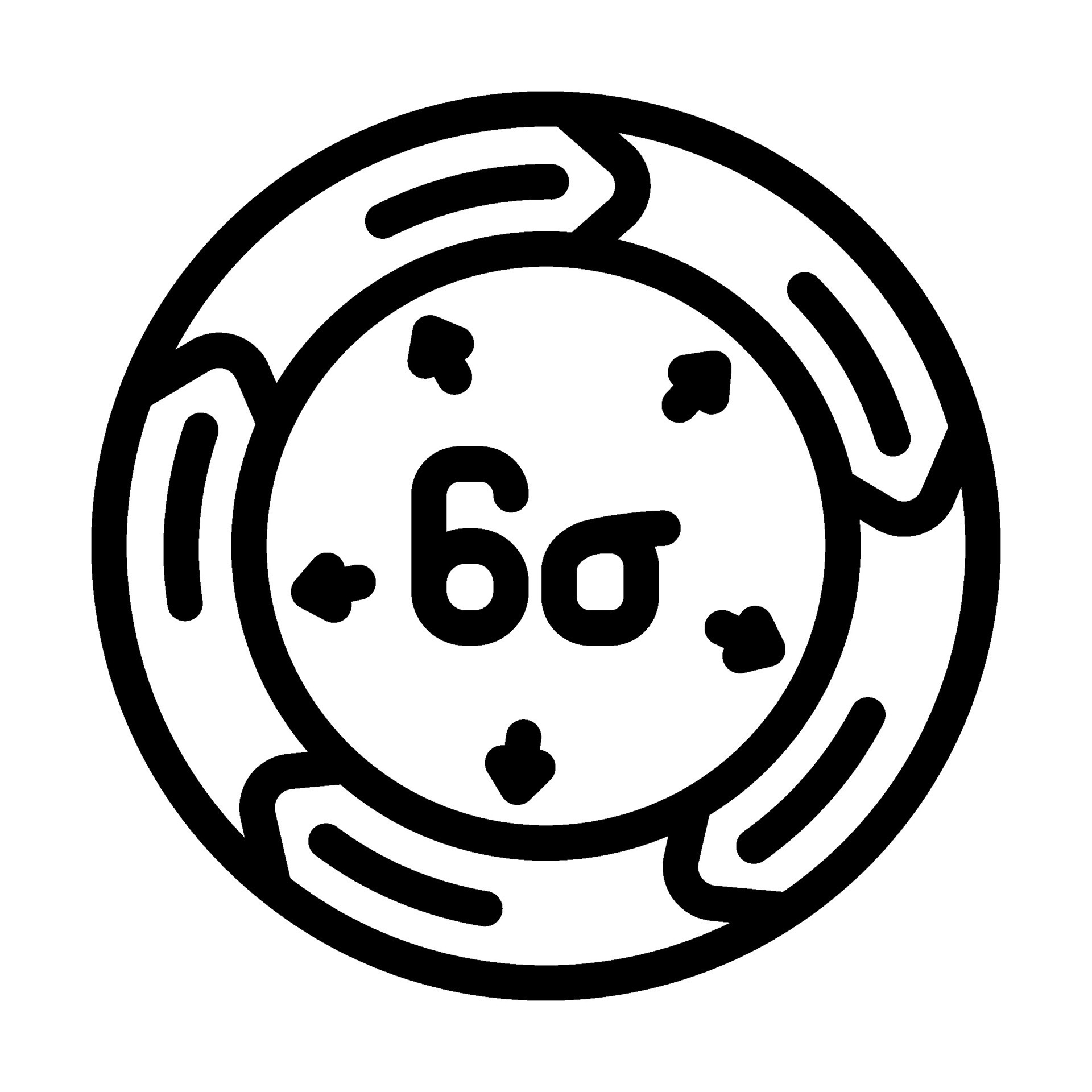
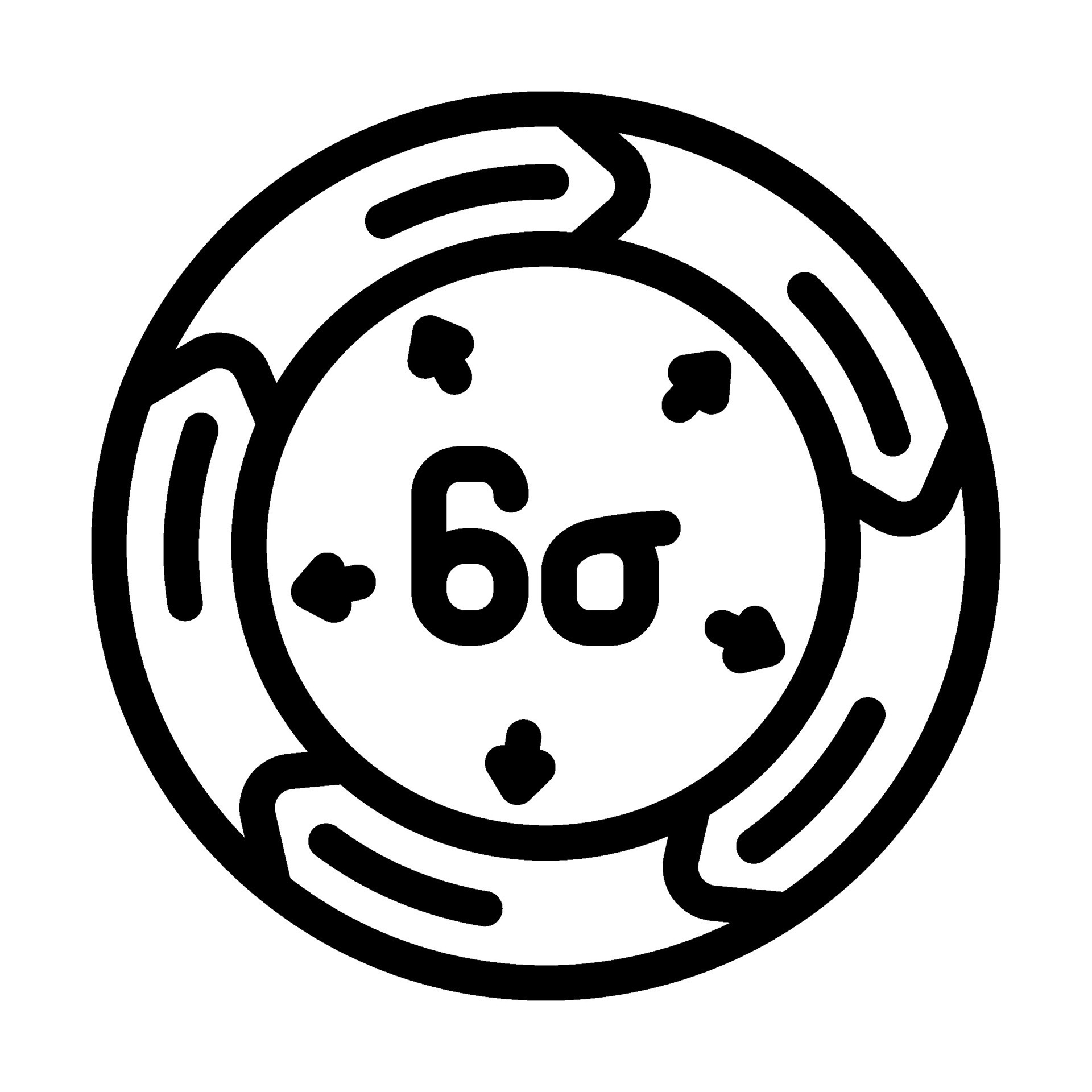
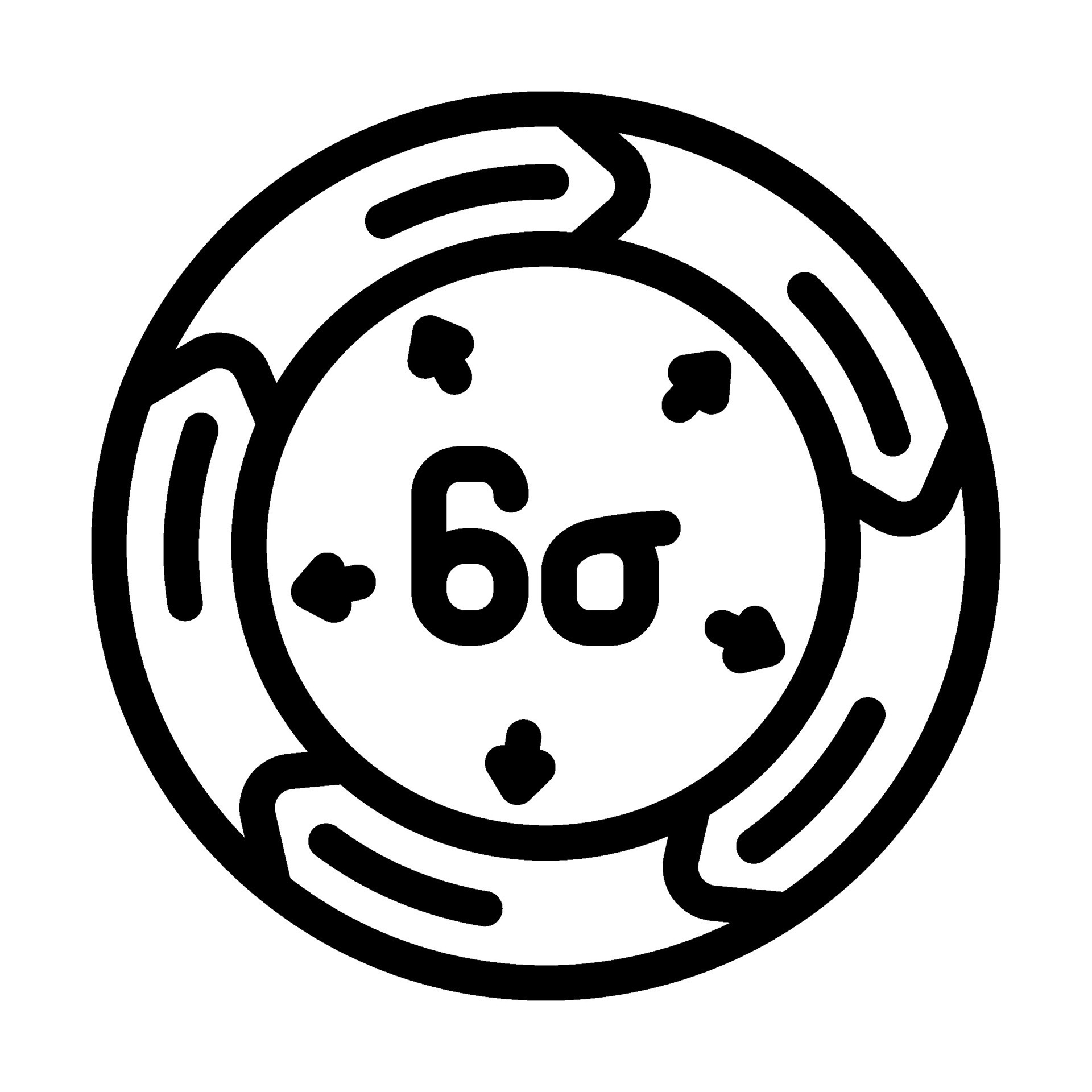
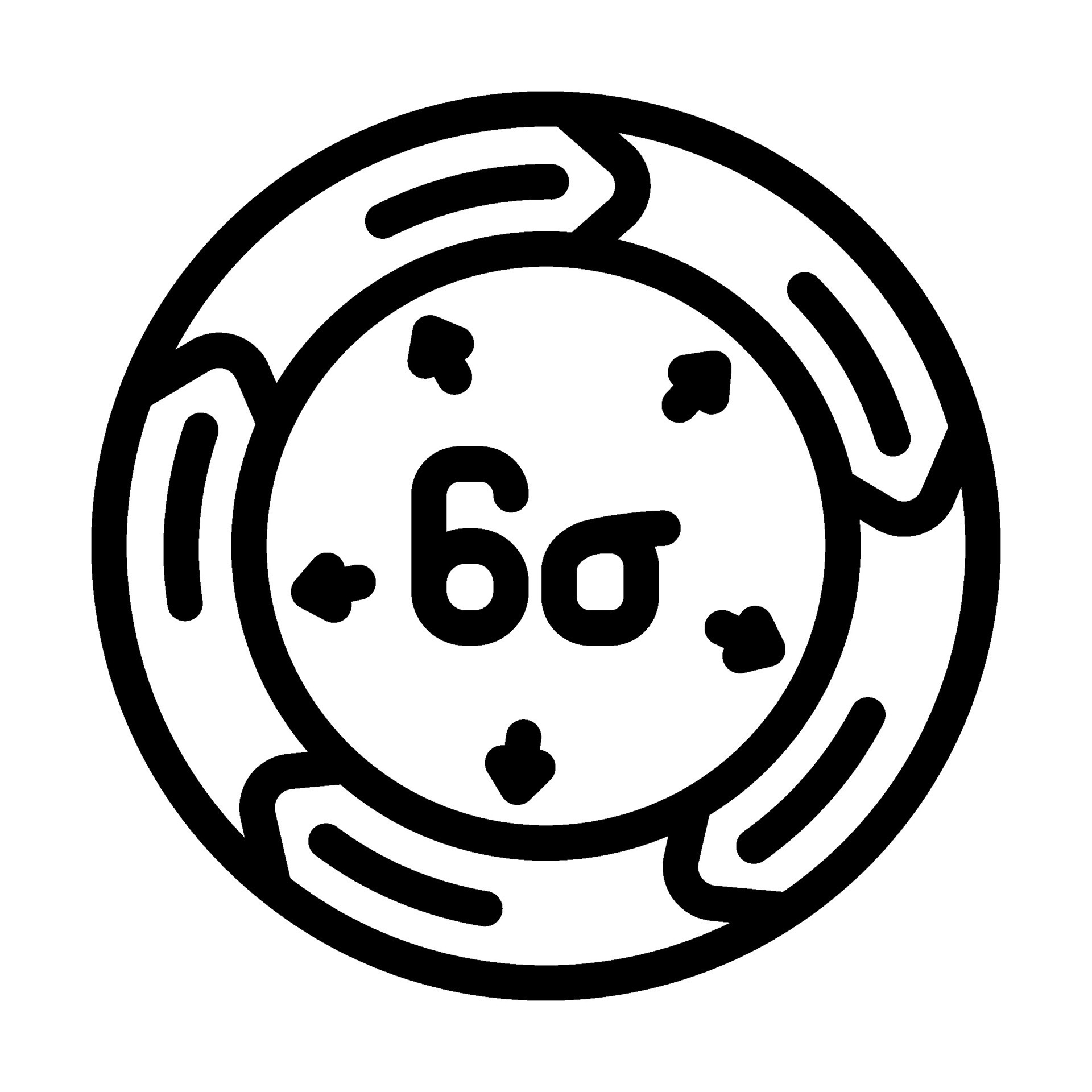